Air compressors offer great versatility and convenience, making them perfect additions to your garage workshop. It doesn’t matter whether you’re a professional or a DIYer, air compressors are bound to make your projects easier to complete, and in most cases, of a higher quality.
Choosing the right compressor for your garage is just a small detail, while the majority of the task lies in creating an effective plumbing setup that is able to cater to the garage space. The dilemma for many people is how to run their compressed air lines, and so, this article will provide you with all the relevant information on how to run air compressor lines in garage.
Table of Contents
- Running Air Compressor Lines in Garage
- Types of Compressed Air Lines Setups
- Compressed Air Lines Sizing
- Compressed Air Lines Materials
- Tools Needed for Running Air Compressor Lines in Garage Workshop
- Running Air Compressor Lines in Garage Workshop Tips
- FAQs (Frequently Asked Questions)
Running Air Compressor Lines in Garage
The very first step to effectively running air compressor lines in a garage space is planning out your optimum layout, and this will largely depend on where you intend to use the compressed air and the number of drops you plan to include in the setup.
Of course, the centerpiece of any pneumatic system is the air compressor, so make sure you’re purchasing one that fits your needs and will last a long time. The main thing you want to look at is the CFM (cubic feet per minute) and PSI (pounds per square inch) that the compressor provides.
Also, you should consider the following questions to help you make the right decision: How important is noise control? Do you want built-in protections? What’s the energy usage? What capacity tank do you need? Are you looking for an oil-free pump? How much maintenance will it require? Carefully think through all operational aspects before picking the right compressor for you.
Visit this guide on sizing an air compressor for more information!
In general, a linear setup is best suited if you intend to have drops on one or two garage walls. Otherwise, you should consider opting for a closed-loop system, which comprises a pipe that forms a curve by coming in contact with the garage walls, along the outside, allowing you to have as many drops as you wish.
Linear setups tend to be the less tedious of the two, as it comprises a single pipe running from one point in the garage to another.
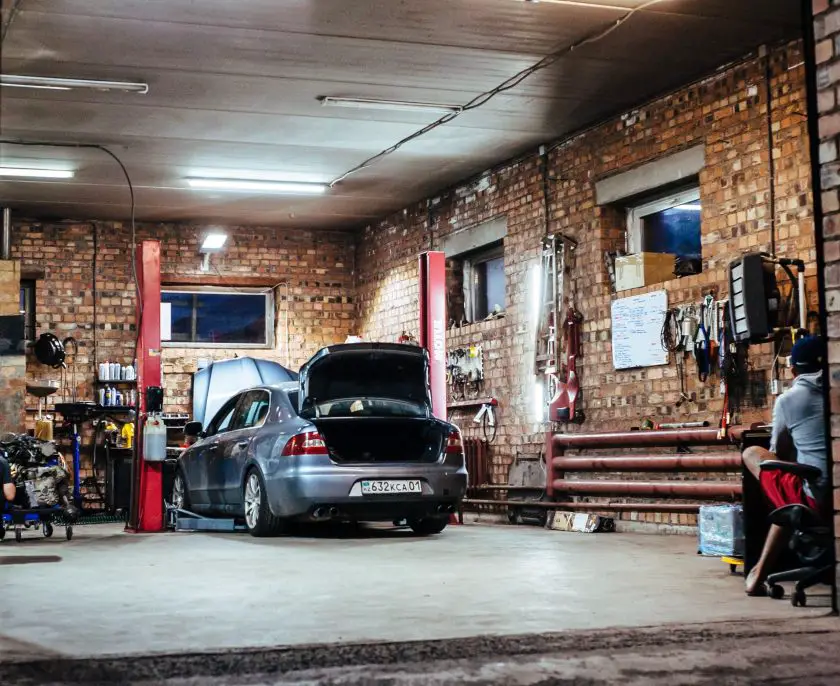
Types of Compressed Air Lines Setups
As mentioned, the two most commonly used compressed air pipe setups are either:
- Linear systems
- Closed loop systems
Linear Compressed Air Line Systems
Linear systems entail a single pipe running from one spot to another without any form of diversions. These types of setups are far less demanding and most ideal for a lot of people, especially when there is limited garage space or a lack of pipe length.
Advantages of Linear Compressed Air Line Systems
- Very suitable for smaller sized garages
- Overhead setup is very suitable for garages with limited space
- Less demanding running system
- These types of systems are seen as economical because they require short lengths of pipe
Disadvantages of Linear Compressed Air Line Systems
- Not particularly suitable for large garage spaces that can handle multiple applications simultaneously
Linear systems can also vary from garage to garage, as you have a few layout options you can choose from.
Overhead Linear Compressed Air Line Setup
The overhead linear compressed air line setup uses a single pipe with a suspended air hose reel at the other end for convenience and compressed air availability. The idea here is that you still have one drop, but you avoid the hassle of having to constantly drag the air hose to different parts of the garage along the floor.
Having the air hose overhead, allows you to reach various parts of the garage while eliminating the risk of stumbling over compressed air hoses on the floor, and generally saving space in your garage.
Side Wall Linear Compressed Air Line Setup
Side wall linear compressed air line setups are best suited to situations where garage space is very limited, and generally involves running pipe through a garage wall. The compressed air pipe should be connected to the mains system via a hose that passes through an air filter. One end of the pipe should be attached to a regulator and the air hose reel, which then delivers the air to your equipment.
Closed-Loop Compressed Air Line Systems
Closed-loop compressed airline systems require more detail when compared with linear setups. If you have a large garage space, then it’s likely that you intend to include multiple drops on all garage walls so that you can have compressed air in multiple locations. This is where the closed-loop compressed air line systems.
Compressed air pipes in these setups cut across the garage walls to sustain multiple pressure drops. The system prevents some drops from being too far away from the air compressor, and the pressure drop that would otherwise occur if the drop was far from the compressor. Strategically locating enough shut-off valves is very important in these setups for the utmost convenience during system maintenance.
Shut-off valves are important features to allow you to shut off air to the entire system in cases of an emergency or for maintenance. In a situation where your plumbing gets damaged, potentially bursting, you can immediately shut off the ball valve so that only the air that remains in the lines is able to escape, instead of having to wait for the entire compressor tank to empty.
They are also very beneficial when you need to make a repair or change to your compressed air line system, as you can shut off air to that specific area and conduct the needed maintenance without having to wait for the whole system to drain.
Shut-off valves are often referred to as ball valves, and when selecting one, you should look for the ball valve to have an internal diameter that matches your piping. If you plan to attach the ball valve directly to your air compressor, you will need an appropriately sized reducer as the air compressor outlet tends to be larger than you need.
Advantages of Closed-Loop Compressed Air Line Systems
- Even pressure distribution is guaranteed despite having multiple drops
- The system minimizes pressure loss
- Tend to be very energy efficient
- Ideal for large garages that conduct multiple applications together
Disadvantages of Closed-Loop Compressed Air Line Systems
- They could be expensive as they require a fair amount of pipe length
- Installing these systems is a lot more hard work
Compressed Air Lines In the Wall vs On the Wall
Many people ponder the question of whether it is worth running your airlines through the walls of your garage, just like water lines are plumbed all over the household. Of course, this will provide a neat aesthetic to your garage in that there aren’t pipes running along the walls, as long as you ensure that they are leak-free.
Many DIYers have spoken out about leak problems they’ve faced after installing their compressed air lines in the wall, but these issues can be solved if all connections are made properly with PTFE tape/dope ensuring a tight connection.
One thing to consider is that running your airlines through the wall will make it a more permanent fixture, providing you with a greater challenge to make changes if you ever needed to. You also need to ensure that the holes you’re creating to run the lines through are also not compromising the structural integrity of the walls themselves.
Compressed Air Lines Sizing
The required airline pipe size for your system depends on the distance from the air compressor to your application and the volume of air being carried to the application. This also will depend on how big your garage workshop is, or how much of it you intend to run your airlines into!
If your pneumatic tools are located on the other side of your garage, you would need a different size pipe than you would if your tools were only a couple of feet away from the compressor. Likewise, the diameter of the pipe could also differ if the application requires continuous high-intensity airflow or intermittent low-intensity airflow.
In many cases, compressed air lines are selected to match the diameter of the outlet on the compressor, which seems reasonable and intuitive. However, this can lead to pressure drops and losses of efficiency within the airline setup.
Any internet search will provide you with charts that show the ratings of a system’s SCFM, and the correct corresponding compressed air pipe size. These ratings tend to be based on the length of the pipes and the system’s psi or its flow rate in SCFM.
Visit our What Is SCFM on an Air Compressor? SCFM Rating Guide & What Is CFM on Air Compressors? What Does CFM Mean? Guide to learn more.
I will provide an example of one of these charts below, but it is important to note that these can be inconsistent, and you should conduct further research into your requirements to ensure you choose the right size.
Airflow (CFM) | 25 FT Pipe | 50 FT Pipe | 75 FT Pipe | 100 FT Pipe |
---|---|---|---|---|
5 | 1/2″ | 1/2″ | 1/2″ | 1/2″ |
10 | 1/2″ | 1/2″ | 1/2″ | 1/2″ |
15 | 1/2″ | 1/2″ | 1/2″ | 1/2″ |
20 | 1/2″ | 1/2″ | 3/4″ | 3/4″ |
25 | 1/2″ | 3/4″ | 3/4″ | 3/4″ |
30 | 1/2″ | 3/4″ | 3/4″ | 3/4″ |
35 | 3/4″ | 3/4″ | 3/4″ | 3/4″ |
40 | 3/4″ | 3/4″ | 3/4″ | 1″ |
45 | 3/4″ | 3/4″ | 1″ | 1″ |
50 | 3/4″ | 1″ | 1″ | 1″ |
Compressed Air Lines Materials
An important consideration for running compressed air lines in garage is what pipe material you will use. Each type of material offers its own advantages and disadvantages, as well as varying fittings and methods of installation.
Here is a list of suitable compressed piping materials:
- Copper pipe
- Aluminum pipe
- Galvanized steel pipe
- Black iron pipe
- Polyethylene tube
- Nylon tube
Let’s take a look at these in more detail!
Copper Compressed Air Pipes
Copper compressed air piping is very commonly used, and will typically be recommended by many compressed air users. It’s possible to obtain very clean air with copper systems and it’s very easy to get your hands on the necessary fittings.
The big drawback is the installation process, soldering. You need some amount of experience to solder copper successfully and ensure that the joints are of high quality and work very well.
If you are able to solder the joints effectively, you will likely never experience air leaks, which will provide you with great energy savings throughout the system’s life. Another drawback is the price of copper, which has continued to rise in recent years.
Advantages of Copper Compressed Air Pipes
- High-quality air can be delivered through them
- Boast terrific corrosion resitance and resistance to rusting
Disadvantages of Copper Compressed Air Pipes
- The significant and continued increase in copper piping costs
- Can face difficulties if you were to need to amend or change the system due to the soldered joints
Aluminum Compressed Air Pipes
Aluminum is a lightweight compressed air piping option that can be easily manipulated when compared to other piping options, making it a leading choice for compressed air garage setups. Aluminum also boasts terrific corrosion resistance which makes it very admirable.
What really makes aluminum so attractive, is that the systems are highly modular and can be installed with a lot of ease, using standard fittings, and not requiring the time-consuming soldering that copper does.
Advantages of Compressed Air Pipes
- Piping is lightweight and easy to install
- Boasts terrific corrosion resistance
- Capable of offering a high resistance against leaks when fitting properly
Disadvantages of Compressed Air Pipes
- Once again, difficult to make amendments to the system once it is in place
Galvanized Steel Compressed Air Pipes
Galvanized steel compressed air piping is a strong and durable material, with the galvanization of the steel significantly increasing its corrosion resistance. This makes galvanized steel a popular choice for some, especially older systems, but if you were to ask the masses, I’m sure it would be advised against being used.
It’s important to understand that the galvanized coating which makes galvanized steel, galvanized steel, degrades over time. As this zinc coating degrades, it will be to flake off inside the piping and eventually cause blockages or fouling within the compressed air lines.
Advantages of Galvanized Steel Compressed Air Pipes
- Has great strength and durability
- Boasts terrific corrosion resistance
Disadvantages of Galvanized Steel Compressed Air Pipes
- The galvanzied coating degrades over time causing blockages and fouling
Black Iron Compressed Air Pipes
Black iron compressed air piping is another material, like galvanized steel, that was often seen as a standard material for compressed air setups before now. It offers great strength and durability traits but is nowadays often described as being outdated.
Modern-day compressed air system designers tend to opt away from black iron piping due to concerns that they allow moisture to condense within the pipes easier than alternatives. The moisture content leads to rusting which will ultimately cause damage to the system.
Advantages of Black Iron Compressed Air Pipes
- Offers great strength and durablity
Disadvantages of Black Iron Compressed Air Pipes
- Tends to be a heavy material which is difficult to cut and join
- Liable to leaks
- Susceptible to corrosion from moisture and therefore rusting
Polyethylene Compressed Air Tubes
Polyethylene compressed air tubing is a low-cost alternative to the metal options. Along with being extremely easy to install with easy plumbing fittings, it also does not react to moisture in the compressed air.
The drawback with polyethylene tubes is that if you require large volumes of air, you will not be able to get a tube that is a suitable size that has high airflow. If you bend polyethylene, it tends to leave a permanent kink and a weak spot in the tubing which can later result in issues. It is not abrasive resistant, meaning you would not use polyethylene tubes as an airline to an air tool.
Advantages of Polyethylene Compressed Air Tubes
- Provides great corrosion resistance as well as not degrading with oil and lubricants
- Lightweight material that is easy to install and at a relatively low cost
Disadvantages of Polyethylene Compressed Air Tubes
- Doesn’t have as great strength and durability when compared to metal alternatives
- Cannot be bent as it will kink
- Typically restricted sizes so is only suitable to certain demands
Nylon Compressed Air Tubes
Nylon compressed air tubing offers an enhanced range of capabilities in that it boasts higher operating pressures than other plastics and chemical compatibility. One of the most popular brands to look out for is Rapidair, which specializes in nylon tubing specifically made for compressed airlines.
Advantages of Nylon Compressed Air Tubes
- Flexible and lightweight material which has suitable toughness for high operating pressures
- Boasts excellent abrasion and corrosion resistance
- UV stabilized material, thus, can be exposed to UV while other plastics may not
Disadvantages of Nylon Compressed Air Tubes
- Reduced strength and durability when compared to metal alternatives
- Generally costs more than other plastics
- Can be restricted to sizes
These are albeit a few of the material options available for your compressed air lines. To name a few more, there is stainless steel, high-density polyethylene, polyurethane, and more! If you wish to learn more about these, visit our Best Pipe for Air Compressor Lines – Pipe Materials or Air Line Plumbing Guide!
It’s important to recognize materials that aren’t suitable for compressed air lines and ensure that you do not pick them.
For example, PVC and CPVC plastic pipe is not recommended for plumbing compressed air regardless of the source, they could be catastrophic. PVC’s burst threshold lowers the hotter it gets and when PVC lets go it will shatter, and anyone and anything around could get shredded by the explosion of the pipe.
PVC and CPVC piping is not approved by OSHA for compressed air systems so they should certainly be avoided. Stick to plastics that are OSHA approved and are oil-resistant, to ensure that the compressor lubricants can’t degrade them and you face no unnecessary issues.
PEX (cross-linked polyethylene) is another material that should not be used for compressed airlines because it is not rated for so, and is very susceptible to UV damage. Instead, a popular alternative is Pex-Al-Pex which is specifically made for compressed air lines. Pex-Al-Pex contains an aluminum layer that is sandwiched between two of PEX, providing a flexible, bendable, non-corroding, and strong material.
Tools Needed for Running Air Compressor Lines in Garage Workshop
Having a good range and quality of tools can help make your compressed air lines set up a lot easier and faster. Of course, all these tools may not apply to every material, some materials require special tools, instead, see this as a broad list of basic tools needed for compressed airlines:
- tape measure
- PTFE tape and pipe dope
- 24″ magnet square
- wire brush
- pipe cutter
- hand threader
- pipe wrench
- pipe vise
- brackets & screws
- screwdriver
- crimp rings
- crimping tool
- cramp tool
- soldering kit
- soldering torch
Running Air Compressor Lines in Garage Workshop Tips
When it comes to running your air compressor lines in your garage workshop, there are a few things you must consider and ensure you cater to, to create an optimum setup in your garage. These tips are:
- Strategically locate your air compressor
- drain and refill the engine oil regularly
- put on the appropriate attire when using the compressor
- use quick disconnect fittings
- ideally you should aim for as few elbows, tee’s and connections as possible
- check for any leaks and tighten loose parts
- add filters as close to the air outlets as possible to account for pipe corrosion or debris
- you should design the system so that there are no low spots where water condensate is allowed to collect
- insert a ball/shut-off valve at the outlet of the compressor and at each drop
- use a soft connection from your compressor to the pipe to help control vibrations
- appropriately size your piping based on your SCFM output
- aim to run around 25 feet of piping before your first drop so that the air cools down allowing the moisture to condense into liquid and be caught in the filters/water separators
- the horizontal piping running around your garage or workshop should not be completely level – and instead slope slightly downwards to help with the airflow
- drops should be installed so that they all run off the top of the horizontal pipe and curve back down – to help gravity assist in reducing water entering the drops
- install unions in numerous locations if using copper, aluminium or steel for ease of maintenance if necessary
FAQs (Frequently Asked Questions)
To run an airline in your garage you must first pick a suitable place to install your air compressor, near a wall socket and out of the way. You can then run a piping network across the walls and/or ceiling to create drops at different locations in the garage to save yourself from having air hoses spread along your floor.
The first step to plumbing a garage for compressed is selecting a suitable location for the air compressor, before designing the layout of your system from this point, and all the components you will need and where. After this, you should calculate the CFM requirements of your intended tools and then select an air compressor that is suitable. You can then select your pipe material, and all the relevant fittings before going forth and plumbing your compressed air system into place in your garage.
The most suitable airlines to use in your garage are likely to be the most popular choices in copper, aluminum, nylon, or pex-al-pex. But, it is possible to use galvanized or stainless steel, black iron, ABS, polyethylene, and more. As long as the material is rated for compressed air use and meets your requirements for size and strength/durability characteristics.
If you have any questions related to running air compressor lines in your garage workshop, feel free to comment below, with photos if applicable, so someone can help you!