So you’ve got two compressors and one compressor tank, and you are wondering how to plumb them up?
While this is a compressor issue that most folks won’t have to deal with, some folks with smaller compressors, like those used for air brush painting, might want to add a tank to a couple of compressors that don’t come with tanks.
Most compressors come with some sort of pressure switch to shut them off when the tank pressure reaches the cut out set point. You have to ensure that your air compressors both have pressure switches that will shut them down when the pressure reaches cut out, and preferably, have adjustable pressures switches if you are trying to plumb two compressors together.
Note that your compressor(s) may run longer than normal due to the fact that they have to fill a tank to the cut off pressure before the compressor stops.This has ramifications for compressor duty cycle.
What is the compressor duty cycle?
Some compressors have a true 100% duty cycle, meaning that they can run and run, and not overheat and cause damage to the motor. Some compressors have limited duty cycle, meaning that if you run them too long, they can be damaged due to heat buildup.
Not sure about the duty cycle of your compressor? If you are not sure, then only run your air compressor in ten minute segments, at which point, you shut the compressor down, and then wait at least ten minutes more before starting it up for the next usage period.
If you don’t pay attention to duty cycle, then you can damage your compressors.
And, if you are trying to plumb two compressors and one compressor tank together, knowing that the compressors will run longer than normal may have an affect on them!
Plumbing two compressors and one compressor tank
Here is how we would plumb two compressors and one compressor tank.
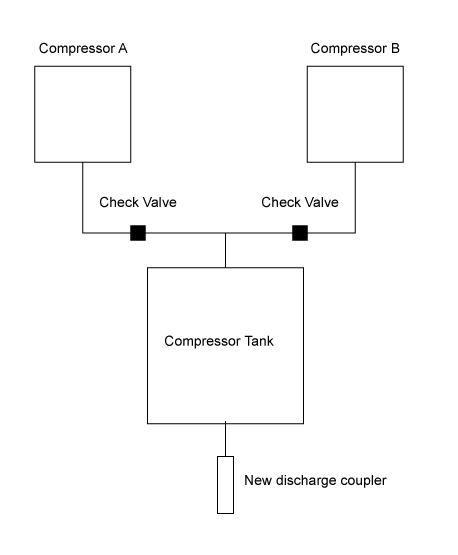
The air compressors each will come equipped with a discharge coupler. This is the plug into which you insert the air line connector to get air to flow from the compressor to the air line.
Both compressors are to be plumbed with a line from their discharge coupler. Each of those lines run through a check valve so that air can flow out of that compressor but not back towards it.
Both lines then connect to a Tee with the outlet from the Tee connecting to the tank.
The tank will have its own discharge coupler into which you would plumb the air line for your air brush spray gun or air tool.
Both compressors on at the same time?
Do you want both air compressors to run at the same time? We wouldn’t. If both compressors have the same cut in and cut out settings however, this is what will happen.
What we would do is set the pressure switch on compressor A to, for example, cut in at 90 PSI. The cut out might be 120 PSI on compressor A.
On compressor B we would set the cut in pressure setting to, for example, 85 PSI with the cut out also at 120 PSI.
Then, as long as air compressor A could keep up with the compressed air demand of the air tool, air compressor B will not cut in.
If air demand exceeds the output capacity of compressor A, the tank pressure will continue to drop until it hits 85 PSI, at which point compressor B would then kick in, adding its capacity to the tank.
If the demand for compressed air exceeded the capacity of both compressors, the tank pressure would continue to drop, and both compressors would continue to run.
Swap compressors?
You might consider swapping out the settings on compressor A and compressor B from time to time, otherwise, compressor A would always be doing the bulk of the work and this has ramifications for compressor maintenance.
If you have questions or comments about this advice, we encourage you to use the form below to post yours.
Okay, so, maybe this is a stupid question; I’m not really a pneumatics guy, but hear me out here:
In the diagram you’ve presented, you’ve basically configured it as a “normal” compressor, just with a binary set of inputs. In a “normal” configuration, as you’ve pointed out, a compressor will run when the pressure sensor determines the stored PSI is outside of the preferred range, yeah? Then maybe we’re making this harder than it needs to be.
Presupposing we had 2 (or indeed, n) of the SAME MOTOR, each running a check valve and the same approximate amount of line. Now (you’d prolly want each on its own circuit for this next bit), say the tank drops to 70 PSI. Normal behavior would be for the sensor to trip, thereby activating the switch to provide current to the motor. Motor huffs and puffs, refills tank until sensor is happy and “untrips” switch.
So why not just hook both motors to the same sensor. Tank hits 70, BOTH kick on, tank simply refills twice as fast, and sensor then “untrips” both. You’d have to be careful not to induce a current sag/power surge, but that’s not rocket science. Hell, use a capacitor and a 1s delay on motor 2.
The MOTORS wouldn’t even know the difference (“am I on? Or off?”). I mean, those tankless compressors can output air no problem (I know, only good for staccato “blasts” of air, but that’s a different matter). The TANK isn’t gonna care either, since once it hits its “safe” zone boundary, sensor kills both motors again.
What am I missing? Why not just disconnect motor 2’s sensor, and run some wires from motor 1’s terminal posts to the now-vacant ones on motor 2? In short, run em parallel instead of in series.
How is this different from me simply replace the 2hp motor on a 100L compressor with a 4hp? So long as the pumps are acting in unison, I would think it’d be identical. Even down to neither carrying an unfair balance of load. I can hook two water pumps up to two streams, plug both into a power strip, and refill a pool twice as fast. Assuming the drain (the tool) can only drain a finite amount of liquid (cfm), as long as I’m pumping faster than it’s draining, I’m good. The spillover (relief valve) will keep the pool from overflowing, right?
If both motors come on at the same time without the separate power supply, you’ll likely blow the fuse / breaker every time. However, how it is written is how I’d do it. You’re good to experiment and if yours is a better way and works, happy for that info and please let us know if it works for you.
What is the best location for the check valves close to the compressor tanks?
Skip, if you are asking about the tank check valve, typically they are installed in the line that goes to the tank, or where the pump line enters the tank. Really though, a one way valve can be installed anywhere between the pump and the tank, as long as the compressor can unload the air over the pump when the compressor stops. If you are not asking about a tank check valve, please provide more info.
Are you saying that each compressor plumbs into the tank through its REGULATED outlet? So, I guess the regulators would always need to be wide open. Would it be any better to plumb them from another unregulated port on the pressure switch?
Yeah, not clear on that. Logically the regulators from each would be removed and just have one on the outlet to the air hose. Plumbing them from an unregulated port on the switch would do it, assuming that the pressure switch base has one. Otherwise, just remove them pre-tank, and add on after.
hello sir i am having 15hp compressor and 20hp compressor connected to one 1000litres tank, how it will works?
Since I thought the “how to” on this page was pretty clear, Guru, please tell me what you mean by “how it will works”? I don’t know what you mean by that.
dear sirs,
in my company I have installed two compressors,one is 37kw motor(star/delta system) and the second one is VSD with 50kw motor and 9m3/min capacity.I have also two tanks with 2m3( parallel conetction).The problem is that I can not secure at least one of the compressors to be in stand by mode.They are in running position all the time.Can you send to me your recommendation for solving this problem.
thanks,
Toni, in order for one of the two compressors not to be running at the same time as the other, on the controls of the one you wish to remain idle, the cut in pressure on the secondary compressor must be set below that of the air compressor you wish to come on when the pressure drops.
In that way, the compressor desired to be on will cycle normally as the pressure rises and falls, and the back up compressor will not come on at all, unless, the primary compressor cannot keep up with the air demand.
As the pressure falls in the primary if air use exceeds the capacity of the primary to fully supply the air, the primary compressor pressure will drop to cut in, but if demand is greater, then the pressure in the tank/system will continue to fall until that pressure reaches the cut in of the secondary compressor, then it will start too.
In the interests of maintenance, it might be a good idea to reverse the two from time to time. Does this help?