The air compressor unloader valve provides a critical function in preparing your air compressor to restart.
A failed air compressor unloader valve is one of the most common reasons why your air compressor cannot restart after you have used air from the compressor tank. When the the air compressor unloader valve is working correctly, the pressure in the tank has dropped to below the normal cut in pressure level of the pressure switch, the pressure switch trips to allow power to flow through it, and the motor starts. If the unloader valve has failed when the motor tries to start quite often the motor will lug (struggle) to start and typically a breaker will trip or a fuse will blow.
What the air compressor unloader valve does
Compressor unloader valves are common pieces of equipment on many types of air compressors including reciprocating, rotary screw and even gasoline or other fossil fueled air compressors.
This Fix My Compressor website is focused on the do it yourself and small workshop air compressor and most of these are reciprocating type air compressors. A reciprocating air compressor will have at least one cylinder, and often may have two or sometimes even three cylinders. Reciprocating air compressors always have an unloader valve.
In the photo below the unloader valve connections are the brass fittings on the left sides of these Lefoo brand pressure switches. The pressure switch on the right incorporates an ON/OFF lever on the right side as well.
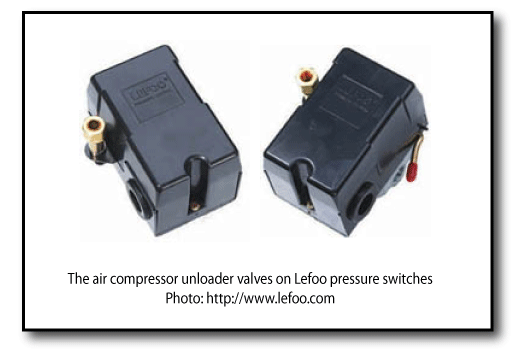
When the reciprocating air compressor reaches the cut out pressure setting the power supply to the compressor motor stops, and as a result, the compressor pump stops. The compressor pump stops, regardless of where the piston in the cylinder is located, and that often means that there is compressed air trapped over the piston when the pump stops on cut out.
On other pages on this site we talk about how marginal a 120 volt air compressor motor really is, and the steps the motor manufacturers must take to ensure that, even with all compressor components working at their best, even being able to start.
If air is trapped over the piston on the air compressor, that adds load to the start circuit. Your 120 volt power supply hasn’t got enough oomph to start the motor without help from a start capacitor anyway, and that additional load on the compressor motor is typically sufficient to prevent the air compressor from starting.
The air compressor unloader valve vents trapped air
What the unloader valve does is that is responds to the compressor pressure switch turning the power off to the motor and allows any air that may be trapped over the piston, or pistons on a multi-cylinder air compressor, to vent to atmosphere, removing any load that the trapped air may have created over the cylinder piston.
How the unloader valve works
The pressure switch may have an external unloader valve like the Lefoo pressure switches above, or it might have an internal unloader valve the the Condor type switch shown below, which incorporates an ON/OFF switch on top though not all of them do.
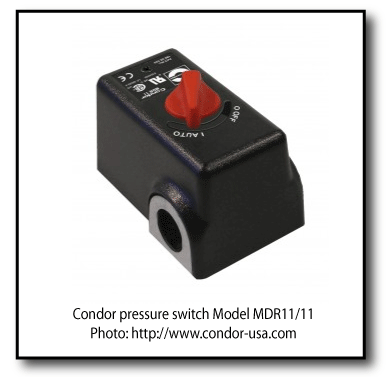
What you cannot see is the air fitting (could be quick connect or another style) underneath the Condor into which the air line from the compressor pump is installed.
Regardless of how the air line from the pump head is connected to the unloader valve in your pressure switch ~ an internal, underneath connection like the Condor or an external connection like the Lefoo (there are more brands, I’ve just used these two popular ones to illustrate the concept) ~ the unloader valves do the same thing.
When the air pressure in the tank reaches the cut out pressure of that pressure switch, the switch trips to off, cutting power to the compressor motor.
Unloader valve opens
The process of turning the power off to the compressor motor is an electro-mechanical one. That means that electricity is driving it, but the end result is a mechanical movement. Something moves inside the pressure switch housing.
What is moving, typically, are a set of points which open and close depending on the pressure in the tank.
The movement of those points is connected to an arm or finger inside or outside of the pressure switch, and that arm or finger pushes or pulls on a small valve pin, which operates the air compressor unloader valve.
When the pin on the unloader valve is depressed, the air path through it is open to atmosphere, and any air trapped over the piston vents out. This happens when the compressor stops or cuts out.
Unloader valve closes
When the pressure in the compressor tank drops to the cut in pressure setting on your pressure switch, the pressure switch will trip again, and this time the arm or finger will typically release the pin on the unloader valve allowing it to shut, and prevent the air that is being compressed from escaping to atmosphere.
There are two unloader valves shown in the photo below. On the left is the Condor version. This unloader would typically be inside the pressure switch with just the brass insert fitting that is on the bottom of this unloader valve showing. The internal arm or finger to operate this unloader is not shown, but the pin which is depressed and released by that internal arm or finger is shown on top.
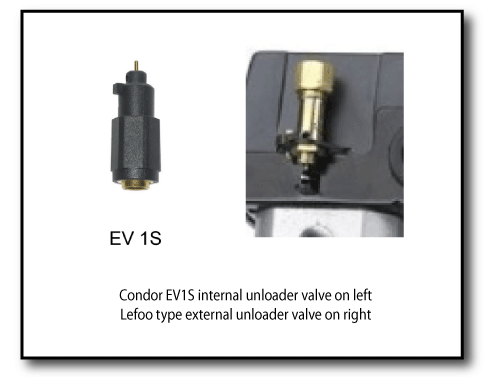
The image on the right just above is the external unloader valve. You can just see the small pin protruding from the bottom of the unloader valve, and that little grey blob just below the pin is the arm or finger extending out from the pressure switch and is what depresses or releases the pin as the pressure switch trips on and off.
What about the air in the compressor tank?
I expect you have a question about unloader valves at this point? That is, when the unloader valve is opened to atmosphere, why doesn’t all the air in the compressor tank escape too? For the answer to that, you will have to see the tank check valve page though we can say that some air compressors unload all the time.
Your comments or questions about air compressor unloader valves are welcome using the form below.
I have a Central Pneumatic 67847 air compressor with LeFoo LF104H .
When the pin on the unloader valve is depressed, the air path through it is open to atmosphere, and any air trapped over the piston vents out. This happens when the compressor stops or cuts out.
Unloader valve closes
When the pressure in the compressor tank drops to the cut in pressure setting on your pressure switch, the pressure switch will trip again, and this time the arm or finger will typically release the pin on the unloader valve allowing it to shut, and prevent the air that is being compressed from escaping to atmosphere.
I don’t understand the last sentence. Does any one have a unloader valve drawing showing how the valve works? Maybe a drawing would help my understanding?
My compressor pump fly wheel cannot be turned once pressure builds up. As pressure rises the motor is having to worki harder until it trips. There is a bleeder valve right at the fly wheel on top of the pump which is letting air out all the time. Once the pressure goes down the motor can turn it again. I guess there is pressure on pistons? It gets unturnable before reaching full pressure. Which part is malfunctioning? What can i replace or do i need new pump?
Hello Jay, I’m experiencing exactly the same problem as you. But I have no air leaks,
Do you have any info to share with me?
Thanks
Tony
Greetings again. I do believe it is my unloader causing the hard start so I am looking to replace it. The direct replacement for Ingersol rand is a hubbel unit, but a lefoo with the same specs is $100 less. IN 20 years I have changed the switch 2 times already and am not sure that the oem style is worth the extra cash this time around.
Is there a way to test the unloader valve? Last week my 5HP motor blew a starting cap on my IR commercial unit. I replaced the cap and it blew a week later. I brought the motor in to a electrical shop and it tests fine. I will have to reassemble the unit for further testing since the motor is now off. The electrical contacts all are clean on the switch which contains an internal unloader that I cannot see, similar to the leefo type pictured above. My plan is to listen for the air release as I manually switch to OFF and then listen for the same once it reaches pressure. Is there any way other than that to test it?
I have a 60 gallon Kobalt, the hose blew out of the unloader valve. My question is, where can I get a replacement valve or would it be safe to reattach the hose?
The answer might depend on why. What is the existing hose made of, Steven? Is it plastic?
Yeah it’s a clear plastic tube that appears to have a threaded sleeve on the end that went into the unloader valve. When I turn the compressor on now it blows air from there and won’t build up enough pressure in the tank.
If there is enough slack, I’d cut the 1st 1/2″ off the tube, replace the sleeve, and tighten it in. If there isn’t enough slack, I’m going to surmise that it’s a 1/4″ tube. You can visit a local industrial compressed air (sells valves, cylinders and fittings) to either ask them for a length of high-heat plastic tube of the same size, or bring the whole tube and fittings with you can ask them to make you another. Just make sure it’s the tube that’s the issue. Let us know if this helps if you would. Cheers.
Hello,
I have a Clarke compressor Model is PP15 ND 50
Its a manual start with a small cut off valve. This releases to allow the compressor to run freely which it does.
If I need to restart the compressor after it has been stopped by an on off ignition switch I have to let all the air out before it will restart by pulling the rope.
I wondered if there was a non electrical cut of valve which also incorporated a manual lever?
Thanks for any advice.
Regards
John
The device in the picture (on the left photo) is what’s known as a cold start valve. These can be replaced if that one has failed. Is this Clarke a petrol driven model? If so, there’s an unloader to load and unload the motor, yes?
Hi, I have a Bambi pt24 which has been working fine until today when I noticed that it wasn’t refilling. I toggle the on/off switch but nothing happens.
UPDATE: Sorted – fuse had gone!!!
Hi, I have Kellogg American compressor, I think 1972 vintage. I have had it for 10 years or so. Its always worked great. Recently it began letting all air out of the tank any time the motor shut off. it will pressurize the tank but will not keep air in the tank. I’ve read posts on check valves & unloader valves because these seem to be common to this problem but I can’t locate these on my compressor. The air leak is on a fitting screwed into the end of the compressor – not sure what component this is. Can you point me in the right direction please? Please see pics attached.
Thanks much,
Alan Edward
Alan, thanks for adding the photos. It always helps to be able to see what the person is talking about. The photo with the arrow, that is a line leading into the end of what I think is the bearing housing, the crankshaft and oil sump? If so, is the small black dot on the bottom of the fitting actually a hole? Is that the leak?
If it is, that suggests to me an oil sump vent and if so, air coming out of there in volume points to the sump being pressurized while the pump is running, and that points to seals / rings on the piston leaking badly.
thank you for the information you have provided. what I am experiencing is the compressor gets up to cut off pressure and the motor stops, but the unloader value is open and lets all the air out until we get to the cut in pressure then the motor starts and the unloader value closes and the compressor get back up to cut off pressure and then the whole process starts again.
Another observation: If when the compressor has reached the cut off pressure and stops, with the unloader value expelling air. I disconnect the power leaving the switch on the top of the pressure switch in the on position (no power) the pressure drops to the cut in level and when it reaches that pressure the unloader value closes and stops, with no air being lost. Interestingly when I turn the switch on the top of the pressure switch to off position ( again still no power from plug) the unloader value continues to expel air again….
First step, check the tank check valve to ensure that it is closing tightly after air enters the tank. Please advise the results.
I not absolutely sure what the “Tank Check Valve” is to be honest, but the tank holds air and not sounds of air rushing out when the unloader is not expelling.
As background I have replaced the pressure switch so I am confident that should be ok. I have not changed the cut off settings on the pressure switch One thing i did observe is some air (low volume) is coming out of the breather from the sump which is used to add more oil.
http://fix-my-compressor.com/compressor-tank-check-valve/
yes i think you right,, i am going to attempt to replace the valve today
i have 3 cylinder 7.5hp renegade compressor. cut out pressure is at 800kpa. once it cuts out, unloader valve opens and as pressure drops to 750kpa compressor starts again. It is continuously doing it. any idea why?
thanks
Jas,
Sounds very similar to my post above. Cant explain why the unloader value opens when it has reached pressure cut off. I suspect it has to open for a second to reduce pressure in cylinder head so it is easy to start again.
Jas, if there is a tank check valve where the line from the pump enters the tank, or somewhere in that line, I suspect that it is not working, allowing all the air in the tank to exit the unloader (which is supposed to be open when the compressor is off) rather than keeping the air in the tank. Please check and add a comment if that’s what the issue is.
I replaced the switch on my compressor. When I try to reconnect unloader hose my compressor bogs down and trips the breaker. If I leave it disconnected it runs fine but there is alot of air coming from unloader hose and compressor doesnt build pressure
Sounds like a couple of problems, Francisco. Bogging down relates to the operation of the compressor pump is overcoming the ability of the motor to run it, the motor slows, overheats, and often goes off on thermal cut out. The air bleeding from the unloader is likely and issue with the tank check valve not sealing properly.
However, when you changed the switch did you do so with one that had similar cut in and cut out pressure settings?
I have an old, bought new from my Snap-On dealer in mid 80’s, but lightly used <10 hrs, Ram-Air gas powered, 5 hp Briggs and Stratton, 20 gallon compressor. The engine runs fine but it wont idle up and when it reaches full pressure and unloads it kills the motor. I'm not sure if the issue is that it wont rev up or that the problem is with the unloader.
I have a small 1.5 HP continuous run compressor and wanted to turn it into non-continuous run. I thought this was just as simple as adding a pressure switch.
The motor is fitted directly on the tank. There are 2 outlets. One has a safety pressure valve connected the other being the outlet. Initially this had just an outlet inline tap and a release valve.
I removed these and connected the new pressure switch to the tank. The type I believe you call a D switch, with the red On/Off button on the top. To the switch outlet ports I connected a safety release valve, and on the line-out a pressure control valve.
I plumbed a copper pipe from the feeder valve outlet back to the other end of the tank where the pressure safety valve is. The compressor starts fine. It builds up to pressure, then switches off the motor as expected. However the feeder valve then opens and vents the air from the tank. When this drops below a set pressure the motor kicks in again and repeats the cycle. How do I prevent the air venting out of the feeder valve, because when it does this I have no pressure in the line out?
Sounds like a good modification except, did you install a tank check valve where the line from the pump enters the tank?
Hi willyr,
In short the answer is No. Unable to do this as the pump/motor is mounted directly onto the tank and feeds directly into the tank and therefore unable to get to any connection between the two.
I have been thinking about this. What if I block the hole on the out feeder valve so it can’t vent the tank. That way, when the pressure switch switches the motor off, it will open the feeder valve without venting the tank, and when the tank pressure drops the back pressure on the feeder valve will then cause the pressure switch to kick in again. Should work ? The only problem is, blocking the feeder valve vent hole so that it can withstand the tank pressure. The ideal solution would be a spot of weld, but I don’t have welding equipment.
Reviewing the thread I see that yours is 15HP compressor? I suspect that a period is missing, and it’s a 1.5 HP compressor, yes?
I find your description confusing as I cannot see what you are referring to. Simply put, when the unloader opens air will vent from over the piston, but if there is no tank check valve air will also vent from the tank until the compressor restarts at the cut in pressure level. You will need a check valve to keep the air in the tank, while at the same time, allowing the pressure switch to monitor the tank pressure to ensure that it’s within limits.
Hi willyr,
Sorry, it is 1..5HP. I don’t understand what you mean by putting a tank check valve in. Even if I could put a valve between the pump and the tank, how can putting a valve between the pump and the tank stop air venting from the pressure switch out feeder valve as the pressure switch is connected directly to the tank.
When the switch switches off, it opens the out feeder valve and vents the air in the tank into the air. I cannot see the point of the out feeder valve having a vent hole. When the tank is empty the feeder valve is closed by the tank pressure feeding back down the feeder tube, When the tank reaches full pressure and the pressure switch switches off, it should then open the out feeder valve instead of venting through the hole in the feeder valve. Hence the vent hole serves no purpose to my mind.
Hi Phillip. If you want the air to stay in the tank when the pressure switch turns the compressor off, there has to be a check valve in the line to stop the tank air from exiting through the pressure switch unloader. This page offers more info on the unloader and how it works.
Hi willyr,
The page link made no difference. what is appears to be saying is that a need a valve in the line before the pressure switch, But how will that stop the pressure switch venting the air in the tank through the feeder valve air vent. When the pressure switch switches off I need to stop the air escaping through the feeder valve air vent so that I have pressure in the line. If I seal the air vent of the feeder valve that will stop air venting into the atmosphere and instead it goes into the line for use. I just don’t understand what you are getting at. It would appear that I have totally mis-understood this whole set up and what I am trying to achieve is not possible. It would appear that the only solution is to put the whole thing back as it was, putting the cost of pressure switch and additional connectors and pipe down to experience and be satisfied with a continuous run compressor.
When you say the “feeder valve air vent” I have no idea what you are talking about.
You have a pump on a tank, and added a pressure switch to enable the pump to cycle on demand. An unloader line is typically part of the process to allow the air over the pump cylinder to escape before the pump needs to restart to refill the tank. If the air over the cylinder is not vented, the pump may not be able to start against that increased load.
The unloader valve opens when the compressor stops to vent that trapped air. If there is no check valve at the tank, then all the tank air will escape through the now-open unloader vent.
If you cannot install a check valve at the tank to stop the tank air from venting, your compressor will continue to lose air.
I don’t know what else I can say, Phillip. If the physical layout makes adding a check valve possible, you’re out of luck. Sorry.
Hi Willyr,
Yes I get that. I plumbed the unloader line from the pressure switch back to the other end of the tank where a pressure safety release valve was fitted, But the unloader valve on the pressure switch, beside having the output line, also has a hole in the side of the valve. So when the pressure switch switches off, it opens the feeder valve, but instead of the air going down the feeder tube and back to the compressor, it goes out of the hole in the side of the valve, and thus empties the tank.
Okay. Compressor to one way valve to T. T goes to tank, T goes to pressure switch. Unloader valve has a separate very small tap going to the pipe *before* the one way valve. This is the one that opens to vent the pressure above the piston.
There is another type with the unloader built in, but off the top of my head I’m not sure how that could work.
I needed my compressor to work. It doesn’t have an unloader valve. I lubricated the belt and increased belt slack so the motor could start, get the belt hot which wicked the oil away and it would grab and could overcome the start force. I don’t recommend this at all, but you gotta do what you gotta do. Even a go-kart centrifugal clutch would work wonders, y’know?
I have a Bambi PT24 that has a leak around the control switch. I have replaced the switch but leak is still there. It seems to be the unloader valve. If I test by disconnecting the unloader the leak is gone – i think the pin in the unloader valve is too long. The new switch came with an unloader valve with a much shorter pin – so I’d like to swap it. Any idea how to remove and fit the unloader valve from the pressure tubing?
Hi David… by way of diagnosing, I take it that the leak is occurring when the compressor is stopped? If it’s while the compressor is running, yup, that’s a problem with the unloader.
However, if air is leaking when the compressor is stopped, ask yourself, where is the air that is leaking coming from? Must be the tank, and that being the case, why is air leaking out of the tank. It’s not supposed to. The answer is, and the typical reason why unloader valves leak when the compressor is off, is that the tank check valve is leaking. Please let us know what’s what with your compressor.
Thanks for the reply. The air starts leaking as the pressure starts to build and leaks whether the compressor is running or stopped. I also came to the conclusion that it must be the one way valve. So that’s the next thing I’ll take a look at. It’s a bit awkwardly placed – will need to remove the compressor motor to get it off! I can see some surface rust inside the joint connecting it to the compressor outlet – so it’s quite likely that the valve has been affected by rust or other gunk too.
You don’t really have to remove the check valve, you can open it up sidely, and replace the o-ring, make sure the spring is working too.
However, if the unloader valve is leaking when the compressor is running, that means air from the pump is escaping out the unloader rather than being driven into the tank. The unloader valve is supposed to be closed when the pressure switch trips to power on and the motor starts.
If the pin is being pushed on, or not released fully when the pressure switch trips, assuming that releasing the pin on your model shuts the unloader off, then yes, you may have to either adjust the pin lever, see if the pin length is adjustable, or replace the unloader. Odd that. If the pressure switch is new, I’d be asking the vendor why the unloader leaks when the compressor is running and asking for a replacement switch.
Please help with my air compressor problem. I have run out of ideas.
It is Maxus EX8401 60 gallon 3.0 HP running. With the tank empty, it runs fine and shuts off at 135psi. When the air is down to 90 psi it tries to restart. Turns over maybe a turn and hums.
If I drop the air down to 50-60psi, it starts slowly but will go to shut off.
I have replaced the start and run capacitors, the check valve and the pressure release valve and switch.
It runs fine with the pump disconnected and with the air line from the pump to the tank disconnected.
Had a repair shop go over the motor and they replace a capacitor (run), bearings and looked it over. Said it was fine and I must have a power issue. Checked voltage and it runs around 240volts, a little higher when straining. Checked amps. Its a 15 amp motor and starts around 12 amps up to 14.5 when it stops.
With air in the tank and before the pressure release valve empties the line, the pump is difficult to turn over, but doesn’t seem to bind. I also cleaned up (sanded) the switch for the start capacitor and looked over the centrifugal switch. Seems fine.
I know the pressure release switch gets the pressure out of the line but the pump is still pushing against 90 psi after a turn or so. Is there a way to tell if the motor just cant handle the load anymore or if its a pump problem?
Was told to check the intake to make sure no air was coming out (none is). Remove air filter and run without and check the line from the pump to the tank to make sure it is getting hot. All checked out.
Thanks
Gary
Try this… if you disconnect the unload line to the unloader valve, and the under 90 psi the motor should start, as you described, then block the unload line by press the hole on the unload tubing, will the motor stop? I don’t think it will, because you mentioned when the tank is empty, it will build up all the way to 135 psi then cutoff, which means the motor or your power source has enough power to push 135 psi into the tank. I still suspect the unloader valve.
Gary, my, you’ve had a trial. Seems that you’ve checked everything that needs to be checked.
I believe, based on what you have written, that it’s an electrical issue. If you are certain that the start and run caps are the right ones for this compressor, and the “motor checks out”, then I have also to go with the power supply.
While I’m not an electrician, I would think that the power draw in amps when the compressor starts would be way higher than the 12 amp start up pressure you are seeing. Please use a browser to see if you can find what the no-load and load start amps are for your make and model of motor. If they are higher than those you are seeing, I would suspect it’s the power supply to the compressor.
willyr
Thanks for the input. It has been trying.
I am running the compressor in a pole barn built last year and I ran the electrical. Had a wiring problem that was supplying only 120v and had the same problem with motor stopping under load. Had an electrician look at it and we fixed the wiring and it ran fine for a couple of months.
I painted a couple of cars and thought it might just be dust, but after cleaning, no improvement. Even tried with air filter off but no help there.
It runs 240 volts at the motor and did not drop to shut down of motor. Rated at 15 amps on a 20 amp circuit. Starts at 12 amp goes up to 14.5 at shut down. I understand that no load is 1/3 of regular amps so my motor should run at 5 amps when disconnected from the pump? Not sure what the readings will tell me? If it runs higher than 5 amps with no load is this a problem?
Thanks again
Gary, I’m afraid that, me not being an electrician, that we’ve reached my knowledge limit. I still think it’s power related, but at this point, it may be time for the electrician route, if no one else can comment with some advice first.
Thanks again. Yesterday I moved the compressor out of the pole bar and into my garage where I have another 240 v outlet. I ran it and shut it down around 80 psi where it is below the restart point but above the 50-60psi point where it was unable to start back up. It struggled but did start and run. My only thought is that I ran some very heavy gauge aluminum wire to my pole barn and it was so thick that I only had a couple of the 5 strands connected to the ground which is necessary for the 240 volt connection. I am going to get an adapter for the thicker wire and see if that helps. Not sure if it makes a difference as I did run two ground poles 8 feet into the ground outside the pole barn and connected to the circuit box.
Thanks again.
Same problem restarting under pressure in new location. Pulled pump and head. Valves look ok. Cylinders are a little scored. My compressor shop told me to run it and close off intake. If it gets loud, its bad rod bearings. I think I’m going to pick up a pump for around $150. I have run out of options. I’ll let you know what happens. Thanks again!
Most welcome. Keep us posted, if you would.
Finally fixed my compressor. It was the pump. I didn’t realize how loud it was until I replaced it. Pulled it apart and everything worked but there were ridges in the cylinder walls making it hard to run. Bought a cheap pump at Harbor Freight for $150. Works great but had a hard time finding one that wasn’t damaged. Probably from packaging a 45 lb iron compressor in cardboard box and shipping. The bad part is that I paid $420 for the 3 hp, 60 gal compressor 15 years ago and spent $370 repairing. $93 to have motor rebuilt, $50 for pressure and on/off switch, $40 for cut off switch and $150 for pump. Plue $18 for 4″ motor pulley, $15 for new belt and had to drill new mounting holes and do a lot of bending on the copper tube from pump to tank. Live and learn. Thanks for the insight.
I have a curtis 15hp dual stage compressor that keeps blowing the breaker at start up. It happens sporadically. any way to confirm if it is the unloader valve ?
Assuming the Curtis compressor has a pressure switch with an unloader valve, the page you posted on talks about that. Is there something about your compressor that doesn’t apply?
I believe the testing method was to drain the tank fully then restart, if it doesn’t trip the breaker its the unloader valve. The prescribed test doesn’t seem to apply as the compressor doesn’t trip the breaker all the time. Is there any other way to test the valve?
Not quite accurate, Eric. The object is to empty the tank, if the compressor starts, then monitor the unloader valve when the compressor reaches cut out and stops, and ensure that the unloader is actually unloading air over the piston. That your compressor starts with an empty tank suggests that it might be the unloader at fault.
Pressure switch :
Seems like unloaded valve (not sure where check valve is?) is blowing off air while compressor runs.
In this case, if there is one, the check valve should be under the 4 way cross NPT connector and 80% in the tank, 20% of it connected the bottom way of the 4 way cross NPT.
… sorry, the check valve is sticking out of the right side of the tank under the pump piston, with tubing going up to connect a 3 way-T, the 3 way T one way goes to the pump piston, one way goes to the front part, you have an arrow state leaking.
(Hi Tony… thanks for your input. Please make the second paragraph clearer for folks… “you have an arrow state leaking”, what does this mean? – Moderator)
My unloader valve (Condor ev 1s) on my husky 26 gallon tank leaks air while the tank is running, then when I turn it off it, bad unloader valve?
Dave, the unloader is supposed to be off while the compressor is running, so that would suggest that it’s leaking… but, that it leaks when the compressor is off points to the tank check valve as the problem then.
I suggest, tank empty and power off, you remove the tank check valve and check it or clean it or discard it and replace it, reassemble, and test again. You may find that fixing the tank check valve leak will resolve both issues. If you aren’t sure about the tank check valve, there’s more information on that part here.
It doesn’t leak at all when the tank is off, only when running
Oh, I thought you said in your original post that it leaked when the compressor was off, too. Well then, it’s pretty much got to be either an issue with the unloader, or the pressure switch and how it’s toggling the unloader open and closed, whether it’s an internal or external to the pressure switch unloader.
You may be able to find a replacement unloader valve (hard to find) though if the problem is to do with the switch and not the unloader, then replacing the switch might be the way to go.
On the other hand, you say it doesn’t leak with the compressor off, how much longer is it taking to fill to cut out than normal, and if not a lot, easier maybe to live with the leak when the compressor is filling?
I have a SpeedAire compressor with a Square D switch. The switch went bad so I replaced it. But with the new switch the Unloader valve just bleeds the tank down until it kicks back on and then the cycle continuously repeats itself. I contacted Grainger (where the switch was ordered from) and told them about the problem and they sent me a new one, but i have the same problem.
Suggestions?
When the air compressor, Speedaire or other brand, is running, the pressure switch has closed the unloader valve, to ensure all the compressed air being generated is sent to the tank. When the tank pressure reaches the cut out pressure setting of the switch, the air compressor stops, AND THAT’S WHEN THE UNLOADER VALVE OPENS. If, then, the air is bleeding out of the unloader valve, the problem is the tank check valve is leaking, not the unloader valve or the pressure switch. Pull the tank check valve (with all air bled off and compressor off, of course} and test, clean or replace the tank check valve.
I have a similar problem to Chris McCullough’s (June 7th), except that my tank *never* fills, the unloader valve simply hisses all air out from the start.
If I block the unloader port on my check valve (which my check valve allows me to do) then the compressor fills with no issue, so I don’t think it’s the check valve. Plus, the check valve is new so it’s unlikely that it’s defective, though I suppose anything’s possible. Is there a way to test the unloader valve?
My unloader valve is a typical lefoo external one, and this is the check valve I purchased: (link removed)
When the air compressor stops, the unloader valve opens to allow any air in the pump to escape to atmosphere.
The unloader valve should be closed… no air should escape, when the compressor is running, regardless of the condition of the tank check valve.
If air is blowing out the unloader valve when the compressor is running, the unloader valve is not being closed. That’s an unloader valve / pressure switch lever issue.
When the compressor stops, no air is being produced. Therefore, the only place air, escaping from the now open unloader valve, can come from is the compressor tank. If that’s happening, then it is the tank check valve that is letting the air out.
There are no other options, Larry.
It’s all very odd I agree. I tested the check valve the way you recommended in another post, by blowing into it. As expected, when I blew in the direction the air is supposed to flow, air came out. When I blew against the direction, from the outlet side back, there was no air coming out, so the check valve did its job.
As mentioned, I have a lefoo pressure switch, a couple of them in fact, and when I connect a line to either of their unloader valves and simply blow, air escapes at their bottom openings, so I’m not sure what’s going on– I thought the unloader valves are supposed to be closed by default, and only open if the switch is hitting their pins?
Hard to believe both unloader valves would be defective, especially since one of the pressure switches is a spare and has never been used?
When the pressure switch has tripped to off, the unloader is always open. The unloader valve closes when the pressure switch trips to send power to the motor, and then the air generated by the pump goes right into the tank, and not out the unloader. When the compressor shuts off at high pressure cut off, the unloader valve opens, and stays open until the compressor starts again. If air is leaking out of the unloader valve continuously when the compressor is stopped, it has to be coming from the tank, and that means that the tank check valve is leaking.
I have already seen many questions regarding unloaded valves that continue to leak air as the compressor is ON (pumping). I am having the same issue myself. However, have already changed out the pressure switch and have gone through THREE brand new unloaded valves and continue to experience the same issues. I am currently using a Condor MDR 11/11 EA rated for 120-150psi. Any “new” suggestions or recommendations for a different switch/valve combo?
It’s not your unloader valve or the pressure switch that is the issue Chris. The issue is that your compressor tank check valve is leaking, and since the unloader valve is open to atmosphere while the compressor is stopped, all the air in the tank will bleed out. Empty tank, remove tank check valve, clean or replace it, and I expect that will resolve the issue. I am sorry that you spent so much money on parts, but they are all good, and can be used as spares. The issue is covered on this website here: http://fix-my-compressor.com/air-continuously-leaks-out-of-the-unloader-valve/
From what the link says if the unloader valve continues to let out air whilst running its the unloader valve? Mine wont fill up. Im stuck on mine, had 3 different pressure switch and 2 different check valves and im all out of ideas.please help
Your what, Steve? What make and model, please? Since you posted on the air compressor unloader valve page, are you of the opinion this is the issue with your air compressor? You say it won’t fill up, but don’t provide any details. What have you checked? Where is the air leaking from, if in fact there is a leak? Or, is you compressor running but the pressure won’t get past a certain pressure. More details, please.
I now have a Condor mdr 1/11, 20a, 11 bar 240v pressure switch. the others pressure switches i had used were cheap off ebay/ amazon.
Its leaking out of one side of the pressure switch near the unloader valve and cables. when i disconnect the 6mm pipe that goes into to the unloader valve there are no other leaks and when i block the end of that hose (the end that goes into the unloader valve) the tank fills with no problems. i have replaced the check valve that seems to be working fine. its a 6ltr tank with a fridge compressor unit on it.
it has worked fine but had to change the pressure switch because the pressure release valve would go off every time the tank was full, so tried going back to the old switch and then that started to leak from the unloader valve too. many thanks
If “Its leaking out of one side of the pressure switch near the unloader valve and cables” and is leaking while the air compressor is off, the only place that the air could be coming from is the tank, and that means that the tank check valve is not seating fully closed, and leaking.
As i said earlier it only leaks when its running. Is there any way the unloader valve can become open e.g electrics trip out?
This pressure switch has the unloader line inserted into the base? If so, push on the line going into the base to be sure it is seated securely. If it’s loose, that could account for air leaking when the compressor is running. If the line is in tight, and it’s truly the unloader that’s leaking when the compressor is running, then it has to be the internal unloader valve portion of the switch that’s failing. Or, the pressure switch isn’t seated tightly enough onto the nipple to the tank, and air is leaking there when the compressor is running.
I have a 12V air tank and compressor I fitted myself a few years ago.
I notice now when I start the compressor the air is leaking out of the dump
valve on the Lefoo regulator while the compressor is running.
Also I noticed a while ago that if I switch the compressor off it does not
dump the pressure but does if it switches itself off.
Dennis, when the Lefoo switches to non-passing power, typically it toggles the unloader valve on the side of it. Is this the type you have? Dump some air, let the compressor start, and watch the unloader toggle when the compressor reaches cut out. Does the lever move and is the pin depressed or released? Your compressor symptoms sure suggest that the unloader valve isn’t working, but if the unloader valve pin isn’t being activated properly, that could lead to the compressor symptoms too.
Hi,
I have an older Craftsman 2 hp 12gal compressor that seems like it needs an unloader valve. It reaches pressure and shuts off but then leaks air until the motor starts again. Checked with Sears and the part is discontinued. It is an external brass unloader valve with a small needle just above the pressure switch. What is the best way to find a suitable replacement.
Unfortunately, I do not have the unit with me currently but will next week.
Below is a picture of the unit.
Thanks
As it says at the bottom of this page, Mike, if the unloader valve leaks when the compressor is off, it’s likely not the unloader valve, but a leaking tank check valve. Please see the page on this site about them, what they do, how they fail, and how to fix ’em.
Thanks for the quick response I will look into it.
I have an unloader , that is venting air to the atmosphere when the compressor is running , after the compressor shuts off it bleeds air for a few seconds then stops. To me if the check valves at the tank were defective the unloader would bleed air continuously. Question , is the unloader suppose to bleed air when the compressor is running? If not what is a possible cause ?
It seems to me that your compressor has a failed unloader valve. When the compressor is running, the unloader valve is supposed to be shut, allowing all air compressed by the pump to be directed to the tank. When the cut out pressure is reached, the compressor stops, the unloader valve opens to allow air to bleed from over the piston, and remains open until the compressor starts again.
Thank you for the advise
Hi, I am putting together a 5 hp 80 gal tank compressor. The compressor is a Westinghouse 2AVC model. It has unloader valves on the compressor. There are copper lines that run from the unloader valves to the oil pump on the front of the compressor. The question I have, do I need to have the unloader valve connection on the pressure switch?
If you have not figured this out yet the unloader valve comes from the oil pump so that low oil pressure would acuate the unloaders possible saving the pump if you run out of oil. Pressure from the tank activates the unloaders through the tube and there is a valve on the front of you pump that shuts off that air pressure when a certain oil pressure is reached. So you are unloaded on start up with high pressure and you stay unloaded until oil pressure closes the air pressure valve and loads the compressor.
John Schaefer says:, that’s the best visual so far! I just bought a Gardner Denver VRV5-8 (Champion) with a magnetic starter setup. I can’t find much online that explains how this is wired, and actually how it works hydraulically. This one has a smooth crankshaft end cover without the unloader sticking out the end. If you could help free my mind, I would be forever grateful. You can answer me on email if you like at randydirt at geemaile dot komp
Hi there. Hmmm, I’m not quite sure why the unloader valve line goes to the oil pump. A photo of the setup would help me, and I expect, anyone else that wants to help you figure it out.
I have a Tahoe gasoline 3 cylinder compressor that will run at idle,how should I adjust the unloader valve to start the compression phase? It is a new unloader valve because I let my brother use it and I suspect that he adjusted the unloader valve and it blew a head gasket on one cylinder of the compressor,which I repaired and it was working as it should until it began to only idle.
We don’t work on gasoline or diesel powered air compressors, sorry. Happy to post this for you in case a kind visitor can comment.
Hoy there! Thanks for this site. I’m installing a small air compressor under the hood of my 4×4 and plumbing it to an air tank. I already have check valves but do I also need an unloader and if so what are my options? It’s a 2 piston with 1/8″ fittings and I’m using 1/4″ ID rubber air hose.
I guess that question is, if the air compressor comes without an unloader valve, why install one? It has a pressure switch to control the ON/OFF, yes? If so, and if the compressor cycles ON and OFF OK, then we suspect that it’s a small, fractional HP compressor motor, and an unloader isn’t necessary… or, under the hood is a small hole in the plumbing from the pump to the tank, and that hole will act as an unloader once the compressor stops.
I have a small Porter Cable twin tank that needed a new unloader valve. The new valve assembly has a quick connect as opposed to a threaded one on the old valve. The unloader tube is threaded though and there does not seem to be a replacement of any sort available that I can find. Is there an adapter for this situation?
We cannot see the image, but here’s what we would do. Visit your local air valve / air cylinder distributor. Google it. Buy from them a couple of inches of tube that is the same OD as the unloader tube. Also get one straight instant fitting, same size tube, with the same male or female thread as the existing unloader tube. Push the new tube into the instant fitting on the unloader, thread the tube for the old unloader onto the fitting, and then push the tube into the instant fitting, and you’ve made a patch. Did it work for you?
I have a dewalt 2 gal. Oil less compressor. It turns on and builds pressure to 150 psi. Then you can hear a small leak coming from the bottom of cylinder piston ring. It also will not recycle on when in use, the motor will just surge but it will not start unless you manually release the pressure to 30 psi.
Bryan, is this the one with the small pin hole near the piston, or does it have a pressure switch with an unloader valve. If it has the pin hole, that pin hole acts as the unloader, venting air over the piston when the compressor stops. If it continues to leak out that hole, then you’ve got a tank check valve issue. As to not restarting, if the unloader (pin hole or valve) is working, then your next step, assuming you are not using an extension cord, is to check the start cap on the motor. See how on this site.
I have a craftsman 150psi 33gal compressor, it will run until full then when it shuts off, air escapes behind the pressure switch in large volumes until the switch tries to turn the motor on again. It won’t start and hums until the circuit breaker triggers. The off / auto switch seems to not work and I cannot get it to restart. I have to unplug the compressor to avoid the breaker from triggering sparking when I remove the plug from the socket. Leaving it sit for awhile it will start again then the process continues. I have replaced the pressure switch and the unloader valve to no avail?
Dan, see the page on air tank check valves, and check to see if yours is leaking. We think it is. If so, clean it up or replace it, and see what symptoms persist. If some do, add a comment here please.
Hello Willyr,
I just bought a Porter Rand 4 h.p. Compressor model CPF 23400S. It works fine but kicks out a 15 amp breaker on every restart. Is it possible for me to add on a decompression valve to this compressor and where and which parts would I buy? Thanks in advance.
Chuck, we’ve never heard of a Porter Rand compressor. Porter Cable has one with this model number, however. As to the decompression valve, if you look at the pressure switch on this model you should see that there is an unloader (decompression) valve on the side of it. You might test it according to the instructions provided on the troubleshooting pages on this site.
Just bought a Harbor Freight 21 gallon air compressor….I have it plugged into a switched outlet 30 amp. It runs fine using the through switch on the compressor but not if I use the wall switch. It seems that this model has the unloader valve built into the through switch on the pressure switch. Is there a way to install a automatic unloader so I can use my wall switch……?
Thank You Brian
The pressure switch cycles the compressor ON and OFF as the tank pressure changes. In order for the pressure switch to turn the compressor motor on, power must be flowing to the switch from the wall plug. If you have a switch in the circuit that cuts the power to the power plug for the compressor, even if the compressor needs to start, it can’t, as no power is flowing to the pressure switch from the supply circuit. If you turn the wall switch on, and power is now supplied to the compressor pressure switch, and that switch is tripped to passing, the compressor motor should start. If you have cut the power to the pressure switch mid-fill, then the compressor will stop. Now it has air over the piston, which will overload the start and perhaps not allow the compressor to go. Either let the compressor run to fill and shut down before cutting off the wall switch, or install an 2/2 120 volt air valve in the unloader line, powered through the supply wire from the wall switch, so that when you turn off the switch the valve opens and dumps the air over the piston.
I have small air compressor with electric motor, the problem is tube that connect check valve to unloader valve is broken and i can’t find similiar tube around my place. can i change that tube with ordinary pneumatic tube?
Pretty much covered on this page, Faisal. http://fix-my-compressor.com/can-i-plug-the-line-to-the-pressure-switch/
Thank you very much, that page answer my question
Why does the unloader port need a line to take it to the switch/shut-off??? All it does is let a little relief out, why not just have it release at the check valve area. Why the need for the line going to switch box, it doesn’t operate anything.
Thank You
We thought that was covered on the air compressor unloader valve Michael (which is where we have moved your post to). I guess we weren’t clear?
When a compressor stops, air is often trapped over the piston. If that air remains, when the compressor tries to start, the motor may not be able to overcome the additional load of the trapped air, and a fuse may blow or a thermal cut out might shut down the motor. The trapped air has to be vented.
Unless you have a really small air compressor that vents air all the time the compressor is running through a small hole in the line to the tank, the venting of air over the piston takes place when the compressor stops. The venting, or unloading, is accomplished by opening a small air valve – appropriately known as the unloader valve – which allows a path of air from over the piston to atmosphere. The unloader actually opens a path for the air in the tank too, however the tank check valve traps the compressed air in the tank, and keeps it there, even though the unloader valve is open to atmosphere.
In other words, the compressor must vent air from over the piston when the compressor is stopped, but not vent air (unless it’s a really small compressor) to atmosphere while the compressor is running.
Hope this makes sense.
To do this, there must be a valve involved, and rather than adding another valve at the tank check valve area, and installing a mechanism for turning it on and off, many air compressors incorporate the movement created within the compressor pressure switch as the points open and close, which has to cycle to turn the compressor on and off anyway, to also open and close the unloader valve.
Of course, the air line from the pump head also has to be plumbed over to the unloader valve which is, typically, on the side of or inside the pressure switch.
And that’s why that line exists.
The air compressor unloader valve first start unloading after ca. 20 seconds after cut off it’s a condor mdr2 aev2s unloader valve can you help
When the air compressor is off, the unloader valve should be open all the time. It opens at cut off to dump any trapped air over the compressor piston, and then it stays open until the pressure switch trips to ON to allow power to flow to the compressor motor and start the compressor. If the unloader valve is leaking air all the time the compressor is off, then it is likely that your tank check valve is not sealing properly.
the unloader valve opens first after 20 seconds so the engine can start it’s been a long wait, it’s a whole new condor MDR 2s with AEV 2s unloader valve sincerely Ole
Hi guys, each time my silent oil-less compressor fills up the tank and cut off, the unloader valve makes an annoying loud burst of air. I wonder is there such a thing silent (quieter) unloader valve that I can replace it? Or is there a way to fix a muffler/silencer to the valve? Its an internal unloader seated inside the pressure switch behind the 2 electrical wire ports.
We don’t know of any pressure switch with integral unloader that has a muffler, Wong. Given how the pressure switches with internal unloaders are plumbed, and even the ones with the unloader valve on the outside for that matter, attaching some sort of muffler is problematical. If the noise is really ornery, use a longer hose from the compressor, and put it under the work bench or in the corner, or some such?
Hi willyr, thanks for the reply. You were spot on how the bleeder valve seated deeply in the pressure switch unit, is impossible to fix any silencer/muffler. Sadly due to space constraint in my airbrushing room, there is no where I can relocate this 0.75hp w/ 8Gal tank compressor, sigh gotta live with the loud short burst.
look at the way silent aire does it, they connect the vent of the unloader valve to a hose that goes back to the compressor. low side. in a super silent compressor it goes back to the tank like the air intake.
Hello,
I was wondering….can a plastic unloader valve be replaced with a brass one? Can an unloader valve be replaced by any other type? I have a Kobalt TQ3126 and the unloader valve failed. It looks like it shorted (black residue under the pressure switch). The tubing that connects to the compressor inlet piping split open.
Thanks
Hi Isaac. To answer your questions in order… yes, and yes. As long as the pump unloads when the compressor reaches cut out, it doesn’t care what type of unloader does the job. If you prefer an internal unloader valve, change pressure switches to one that has the internal unloader. If you prefer one with an external unloader, any brand will do as long as you wire the pressure switch correctly, it has the same cut in and cut out and voltage of the original, is plumbed similarly, and you can connect the unloader line to the unloader valve.
Of course, if your compressor is under warranty, you’ll want to use OEM parts to maintain the warranty. Otherwise, use whatever parts work.
I have a Campbell Hausfeld compressor model VT623301AJ with a VT470200KB pump that hadn’t been used in a few years. I fired it up and it has been having difficulty running and will trip the breaker.
This is what I have so far. When the line is open so no pressure will build it starts up immediately and smoothly and runs no problem. If I shut off the line to build pressure you can slowly hear the difference in the pressure load on the pump and eventually it will trip the breaker at ~90 PSI instead of the 125 PSI cutoff. If it has low pressure ~30 PSI in the tank the pump will try to start but before it reaches top rpm it shudders and trips the breaker. At the higher tank pressures 60+ PSI it tries to move under load from what it sounds like and trips the breaker. Now with the tank under pressure and switch off the unloader valve does not leak but when the switch cuts off or is turned off there is a hiss that follows that sounds like the unloader relieving pressure. So is this the unloader or the check valve or some combination of both? Could it even be the start/running capacitor on the electric motor?
Well, we think you’ve determined that it’s not he tank check valve leaking, or a failed unloader, as from your post it sounds like the unloader is working find. We think you may have an electrical issue. First thing to check is to make sure that you’ve got clean power, preferably on a 20 amp circuit, so that the power supply to the compressor is not compromised. If you have any extension cord or power bars into which the compressor is plugged, get them out of the circuit. Plug the compressor directly into the wall socket. If you’ve done this, or this doesn’t help, then we would be looking at the capacitor as being weak or failing. Check that next, and then it may require a motor load check too, but first, we would check the caps. See how that’s done on the page on this site.
This type of unload mechanism won’t work with head unloaders will it? the unloaders on my pump were operated by positive pressure from a pilot unloader valve. Im converting a gas powered job to electric and the whole unloader conversion has me more than a bit confused
Dale.You are correct. The unloaders shown are for compressors powered by an electric motor. Once you get into alternative fuels, the unloader valve does different things. In your compressors case, your unloader adjusts the throttle valve, so that, when the compressor reaches cut out, the motor is throttled back to idle until the demand for more air, and then the motor throttles back up again.
When converting the compressor from gasoline to electric, the unloader valve will then vent air over the piston(s) when the compressor reaches cut out pressure and STOPS, this allowing an easier re-start to the compressor motor when the tank pressure drops and the motor has to start to pump more air.
Hello, i have a sears 31 gal air compressor that starts great, but after it cuts out it is under strain to restart and trips the circuit breaker. It does not hiss when it cuts outs. Any ideas on why this happens? When motor is cool and tank is empty it starts right away. Could this be a unloader or switch problem? Thanks.
Actually, this topic is covered in a number of the pages linked in the compressor problems section on the left of the page, Danny. However, we realize that this issue is not specifically addressed, so here is the new page about why air compressors will not restart when air is used.
Hello. I have an air compressor where the relief valve starts popping open and closed when the compressor shuts off. Would anyone have an idea as to what I can do to repair that? The tag on the valve says, ” A popping relief valve is an indication of excessive interstage pressure.” I’m not sure what that means,or how to fix it. Thanks in advance for your help with this matter.
Kenny
A bit hard to be specific as we have no idea what make or model of air compressor yours is. If the PRV you refer to is in the line between two cylinders, then you quite likely have a problem with the intake valve on the second cylinder.
aloha, , i have a Campbell hausfled 5 hp, 30 gal, (vt629901aj) compressor it has started to develop this straining sound when trying to build up pressure above 80 psi. i have cleaned and checked the valve in the tank, it builds pressure up to 80 psi at normal speed ,then the motor seems to slow to about half speed then it strains further and will stop. at this point i unplug it, , do i need a pressure switch or the unloader vavle, ?any help would be greatly appreciated, thank you john
And Aloha back to you. While there could be many things that may be the cause of the motor straining as back pressure from the tank grows, one of the most common is a failing run / start capacitor. Please see the pages on this site about what they are and how to check them. After doing so, if they are not the cause, please add a comment and we’ll on to the next logical source of the problem.