Compressor oil in the air lines is not good because it indicates that you have a developing problem with your air compressor pump, and it also isn’t good to have compressor oil in the air lines because the oil that lubricates the air compressor pump is not a suitable lubricating oil for other compressed air equipment, including your air tools.
The compressor oil in the air lines will migrate down the lines to all your air using equipment. Depending on what the parts inside the air tools are made of the air compressor oil may interact with them, making seals brittle, or swelling them to the point where the tool may not work properly.
Having compressor oil in the air lines is even more of a problem if the compressed air is flowing through an air filter or lubricator and then on to a high-cycling air valve, many of which may contain plastic components and all of which will likely react negatively to the additives in the compressor lubricating oil.
Caution: Compressor lubricating oil may react with plastic filter bowls
The additives that are in the compressor lubricating oil attack some plastics. Over time, the oil can affect the elasticity of the plastic, increasing brittleness of the filter bowl or lubricator bowl, and causing crazing, cracking, and possibly contributing to bowl failure.
Having a plastic filter or air line lubricator bowl explode under 120 PSI of pressure is not a pleasant thing to be around.
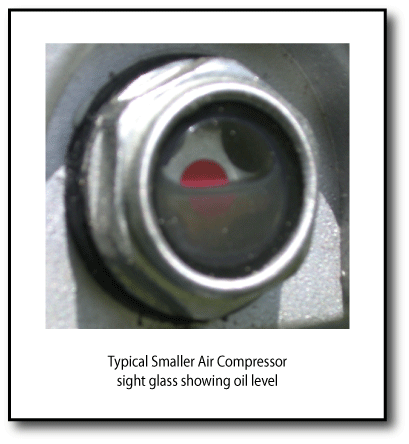
If you have compressor oil in the air lines – and it’s hard to think that any oil lubricated air compressor won’t send some oil into the air – and you have a filter or lubricator with a plastic bowl, we would always recommend installing a metal shroud over the bowl. The metal covering has slots to allow you to see into the bowl without removing the cover, and in the event of a bowl failure, the covering will help to trap plastic debris if the bowl shatters under pressure.
Compressor oil in the air lines and compressor pump problems
Industrial air compressors like rotary screw and vane types have oil separators as part of their standard equipment. Their purpose is to strip any oil used in the compression process and removing that lubricating oil from the air stream before it gets into the lines.
The small workshop air compressor is quite often a reciprocating type with one or more pistons inside of cylinders. The pistons move up and down (reciprocate) inside the cylinders as the compressor runs, alternatively pulling air into the compression chamber and then driving that air into another cylinder or down into the tank.
Many of the lower cost (under $350 or so) oil-lubricated air compressors are lubricated via the splash method. Essentially, moving parts and vibration of the pump splash lubricating oil from the oil sump onto the moving pump parts, including up under the piston and onto the cylinder walls.
What keeps that lubricating oil from getting into the compressed air compression chamber is the piston seal. This wraps the piston, typically moves with it, and as the piston reciprocates inside the cylinder, that piston seal wipes the walls of the cylinder, driving the oil back down into the sump as the piston cycles, keeping the bulk of the oil from getting past the piston and into the compression chamber.
When it is new, that piston seal is very capable of wiping the cylinder wall and keeping almost all of the oil in the sump. When (and that is when, not if) the piston seal wears due to air compressor use, more oil can wick by and into the compression chamber. As the seal wear continues the amount of oil getting into the air increases, and you end up with an increasing amount compressor oil in the air lines, with the concerns noted earlier.
This also generates the need to closely monitor the sump oil level to ensure the pump is adequately lubricated as more and more oil leaves the sump and enters the air going into the compressor tank.
Resolving the problem
Wicking past the piston seals is pretty much the only way that compressor lubricating oil can get into the compressor tank, at least on reciprocating type air compressors.
The upshot of that is the only remedial action is to tear down the pump and replace the seals.
The tendency is to try and get OEM parts which is almost impossible for an air compressor that has been purchased from a discount or big box store.
One source for piston seals is the compressor repair company that your store would send a compressor for repair under warranty, if they do. Check with all the stores that sell compressors and ask where they would get the compressor fixed under warranty. That shop may be able to help getting seals.
There are companies that specialize in providing seals as well, and some research on line will locate those companies. I suspect you will need to be able to provide details of the seal you are trying to replace, so the downside is that your compressor will be pieces while you are searching for a seal replacement, if you haven’t been able to find a seal kit before tearing down the compressor.
One additional note; we would suspect that if the piston seal is worn, then your valves have been well used as well, and since you have the pump apart anyway, we would recommend that your replace the valve plate and the gaskets at the same time.
thank you very informative and very helpful.
Hi
Can you please assist me with my fisheye problem that I got. I recently bought a new 3hp 200l atlas corp compressor brand new filters and brand new airlines and a brand new spraygun and still get fisheyes. My setup is as follow from the compressor 2m airhose runs upwards from there 3m airhose runs to a watertrap then 3m to a pre and after filter then 3m to water and oil regulator and this all runs downwards *- 45 degree. From the regulator a 10m hose to the gun which has a watertrap on it. there are no signs of water but still I get fisheyes. I used a wax and cillicone degreaser and prep all my vehicles before it gets flatted and before it gets sprayed. When I spray the first coat no signs as soon as I put a second wetter coat on everything is smooth until a minute then you see the paint starts seperating which causes fisheyes. I had a compressor tech in today and he said it could be from the compressor standing in the workshop and picking up boddyfiller dust which could cause this problem but I cant see how. Please reply asap, Please help to sortout this problem with the fisheyes. This is a nightmare becaming hell.
Thanks
fisheyes are caused by silicon, your air setup is fine
I don’t disagree that silicone might do it to, I just haven’t had that experience. I can tell you that without question, water in the air line to the paint gun produces “fish eyes” on a paint job. Thanks for the tip.
Sean, I’m not a pro painter, so I cannot comment with any authority on your painting process. In reading your post I interpret this as either the contaminant is being sprayed onto the work piece through the spray gun, or it’s already on the surface. You mention a water trap on the gun. Is this a desiccant water remover? If not, try installing 1) a coalescent filter just before the gun and a desiccant water remover in the port of the spray gun. If you still get fisheyes with that, then I’d have to think the problem is already on the surface or it’s already in the spray gun?
Hi,
I’m at a loss. I have a Kaeser Sk-26 bought it second hand. Its a rotary screw compressor. When I drain my tank at the end of the day I’m discharging moisture as well as oil. What does the oil mean? Am I screwed?
Not necessarily. You need to get into your manual (or get one) and read up on the oil scavenge process… a tube is blocked likely. Your Kaeser symptom relates to this issue more often than not.
problem fixed !
The vendor took back the compressor and gave me a new one. Moreover they told me that the problem was that I switched on the compressor allmost immediately after having filled in the oil while they told me I should have waited for at least 1 hour for the oil to flow down into the sump..otherwise rotating parts in some way splash the filled in oil onto unwanted parts (air inlet?). So this time I followed their advice- which unfortunately is not mentioned in any way in the user manual – and now everything works fine. No more oil coming out from the compressor.
sorry for bothering you once more. I have made another test. I disconnected the air tube that goes from the T-junction to the pressure regulator so that I can see directly what comes out from the compressor before the air enters the tank or the pressure regulator. Of course as I was suspecting oil is spit out from this tube and so I let run the compressor for 20 min with the tube at the T-junction open so that “all” oil that is inside the piston or the connecting tubes can be spit out. Indeed after some 10 min oil stops to exit from the tube at the T-junction. However if I reconnect the tubes at the T-junction and let the compressor run normally once again to build up pressure in the tank – say for 1 hour – and then check again what comes out from the T-junction when I disconnect it once more…again oil is there. The only explanation that i can imagine now is that the piston seals are broken (the compressor is new !) so that oil continuously seeps through the piston seal from the oil sump to the compressor air outlet and this seems to occur more easily if pressure builds up. What seems strange to me is that a new compressor has such a defect.
I have bought silent air compressor and I get a oil mist sprayed out from the pressure switch unloader valve each time the pressure reaches the upper pressure (“cut-out pressure” if I understand right). The compressure is new and I filled the oil level to below the max level. I also have oil smell in the compressed air.
When I read about oil in air lines I removed some oil from the compressor so that the level dropped to the indicated “mid” value on the oil level gauge. Nevertheless oil smell still remains in the compressed air and an oil mist spray continues to exit from the pressure switch unloader valve each time the each time the pressure reaches the upper pressure.
Does it mean I have overfilled the oil ? Will the above problems diminish in a reasonable time if I continue using the compresor and oil exits with the air ?
The oil that is in the tank, in the discharge line to the discharge coupler, and probably in your air lines, will, over time, diminish if no new oil is being added.
In order for oil to be in the discharge line from the compressor tank, it is either coming into that line from the pumping process, or being pulled from the tank as you are using air.
Add a short hose to the discharge coupler and blow off air from a full tank. If you use a blow gun and blow onto a clean piece of paper, you should see if oil is continuing to come out of the hose from the tank, or, if the oil mist / spray is diminishing as the air flows from the tank, that suggests that it’s fresh oil coming from the pump. That being the case, you are getting significant blow-by of oil past the piston seal(s).
Did you follow the break in process according to the manual? That’s important to do to help seat seals among other things.
Actually the oil spray is coming out just from the condor MDR1 pressure regulator switch and only when the motor stops ..there is a unloader valve on the condor MDR1 which ejects excess air pressure when the max pressure has been reached. Oil definitely sprays out from this valve (see circle on image) .
On the other hand no oil sprays out from the compressor discharge coupler. Just some unpleasant smell which to me appears the smell of oil, but perhaps its just the smell of new rubber sealings or the smell of the new tank.
The major problem remains the oil spray coming out from the pressure switch as I said when the motor stops when max pressure is reached. The compressor is an oil-lubed silent air compressor of the fridge compressor type (see picture).
In the user manual no break-in procedure is described. However after your suggestion I did the break-in process, leaving the compressor running for 30 min with the tank drain valve on the bottom of the tank open. By the way no oil nor any water came out from the tank. The tank appears to be clean.
After the break-in procedure I still get the oil spray out from the pressure switch valve. The smell of air appears somewhat changed (perhaps to the better). I cannot tolerate however that the pressure switch produces an oil spray each time the max pressure is reached.
Marco, it’s good that no oil was coming out of the tank drain valve.
So then, if the oil is blasting out of the unloader valve on the bottom of the pressure switch when the compressor unloads, where is that oil coming from?
With the compressor unplugged, pull the cover off the pressure switch and have a look inside. Anything unusual?
If fresh oil is not migrating from the oil sump into the air stream to the tank, which would happen if the sump was too full and the piston seals had not seated, and by the same path into the line to the unloader valve, we are puzzled as to where the oil originates. The only source could be the oil sump.
Since the air compressor is new, what does their support tell you about this oil mist?
I called the support illustrating the problem. They told be that I probably have put too much oil. However I was very careful in controlling that the level well below the max level. Furthermore after I recognized the problem I have removed oil so that now the level is below the medium level. Still the problem persists. I hope that letting the compressor run over many pump start stop cycles the repeated spraying out from the unloader valve will at some point stop , since now the level is below the suggested mean level.
So they suggest that the oil has bypassed the piston seal and into the compression chamber and then into the…. where? If the oil is coming out the unloader valve, and it’s coming from the compression chamber, then some of that oil must have migrated to the tank. You may want to consider a coalescent filter if you see that happening.