There are sometimes great reasons why you might want to connect two air compressors. While a single air compressor may not offer enough flow to supply a higher demand air tool and another, single air compressor, can have the same problem with that same air tool, if you connect two air compressors into one line to the air tool, you may have enough airflow from the two to use that higher demand air tool.
This article will provide you with the necessary information on connecting 2 air compressors together, how to do it, and the most important considerations!
How Compressors Run to Generate Air
A quick review of how compressors work (also covered in detail on a page on this site) is that they have an air tank into which air is pumped. When the tank pressure reaches the cut-out setting of the pressure switch, the pump stops, and nothing else happens until you begin to use the compressed air that’s stored in the compressor tank.
As you use air, the tank air pressure drops. When the tank pressure drops to the pressure switch cut-in level, the pump will start, and add more air to the tank until the tank reaches the cut-out pressure setting, and the pump stops.
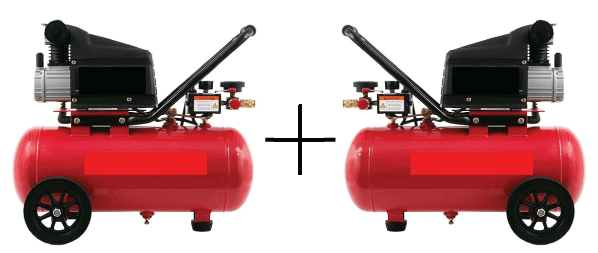
What Does Connecting Two Air Compressors Together Achieve?
However, if your air tool has a greater demand for compressed air than the compressor can deliver you will use air in the tool at a greater rate than the compressor can supply it, and even though the compressor is running, since it cannot keep up with the demand of the air tool, the tank pressure will keep dropping until there is not enough compressed air to run the air tool.
To use a higher-demand air tool you will need a bigger compressor. Or, connecting two air compressors to the same airline to the tool, if you have a couple of small air compressors around, this might work.
In this situation where your air tool requires a greater demand of air at a greater rate than the compressor is capable of supplying, by adding a second air compressor and feeding both into the same line, you will have greater CFM to provide the tool.
Let’s say we have a second air compressor that has the same CFM rating as the first and is the same brand and model, we could double the current CFM rating of the system without any additional control complexities. This is how to connect 2 air compressors together in parallel, or just run 2 air compressors in tandem!
This method for connecting two air compressors together for more CFM pumping capabilities, while also providing a higher CFM at the outlet of the compressors, available for use with your tools.
Here’s a YouTube example of the methods being used!
In some cases, it will also be possible to connect two different make and model air compressors, with different CFM ratings. For instance, you could connect a 5 CFM air compressor with a 10 CFM air compressor and have 15 CFM available!
Here’s a YouTube demonstration that explains this method in more detail!
How to Connect Two Air Compressors Together
If you have two air compressors, select which will be the primary air compressor and plumb a tee into the discharge coupler on that one. At your discretion, you can consider removing the regulator from the line so that the flow to the tee is full pressure.
The tee is set up as: one leg of that tee is the supply from the primary air compressor, one leg of this tee is the supply from the secondary air compressor, and the last leg is where you install the airline to your air tools.
I have picked out a t-style manifold readily available on Amazon that would be perfect for this job. It’s advised when installing one to use quick connect fittings where possible so that you’re able to disconnect and reconnect the system with ease, and whenever required.
- 2-Way air MANIFOLD and splitter with (2) 1/4-inch brass 6-ball couplers
- High corrosion resistance for longer life and smoother operation than standard couplers
- 1/4-inch body plug input with a 1/4-inch body industrial interchange couplers output
- Industrial interchange compatible with industrial, "m", "D", and "I/M" Style plugs and couplers
Last update on 2024-04-15 at 02:12 / Affiliate links / Images from Amazon Product Advertising API
If both air compressor tanks are full of compressed air when you start using your air tool, compressed air will be drawn from both tanks… at least, in theory. The reality is, compressed air always flows through the easiest path from high pressure to low.
As air is drawn from the two compressor tanks to the air tool, compressed air from one tank will flow into the other tank and vice-versa, rather than all of it flowing down the airline to the tool.
By installing a check valve in the line between the secondary air compressor and the tee of the primary compressor. This will prevent air from the main tank and compressor from flowing back into the secondary tank and, if the secondary compressor is not running, air could be lost from that compressor’s unloader valve.
The installation of check valves will be easy as they typically have arrows on them which depict the flow direction! Your setup should have both compressor’s outputs connected to check valves via hoses and then into a t-manifold which then has a hose on its output where you can connect your pneumatic tools.
Once the pressure in the hose to the air tool drops due to air use and the primary compressor tank no longer keeps up, air will be drawn from the secondary tank as well, helping maintain the flow and pressure to the air tool.
If the regulator(s) are removed at the compressor, a regulator should be installed at the point of using the joined supply so that the air tool can be operated at its best efficiency and minimum air use.
Important Considerations
As just touched on, check valves are an important component to consider attaching when connecting two compressors for more CFM. When the secondary air is flowing, once again, air from that second tank could flow back towards the tank of the primary air compressor rather than down the line to the air tool, as air will always flow the path of least resistance.
Solution? Another non-passing valve before the tee in the discharge coupler of the primary compressor, allowing air out of the tank, but not back into it from the other compressor.
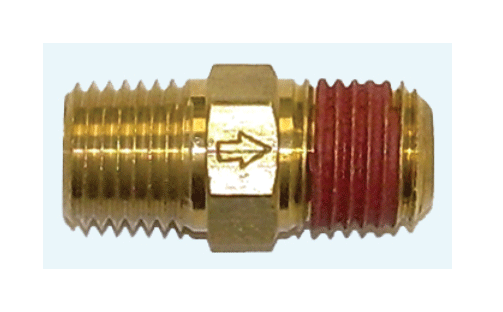
The image above is of a simple, in-line, check valve for compressed air. It’s also known as a non-passing valve. If you Google air check valve you will find many sources with a variety of attachment options.
With the male thread on either end of the check valve in the image, installation is not complex. Note the arrow on the body. That shows the direction that the compressed air can flow through this valve. Take care not to install it backward!
Setting up the two compressors to feed one line will enable work to be performed more successfully with a high-demand air tool but, if the air tool exceeds the capacity of the two air compressors, then it would be time to consider a larger compressor for increased airflow if that tool is to be used a great deal.
Running 2 air compressors in tandem is a great idea for continuous air tool applications as the combined air system now has a higher CFM. It is also suitable for intermittent uses, in cases where specific air tools require a greater CFM than your singular air compressor is capable of providing.
Though, with that being said, connecting two air compressors together with each other for intermittent use only maybe a tad radical. It’s probably worth just buying an additional air tank rather than a full compressor, given that you’re demanding only very short periods of continuous use.
It may also be that buying a new compressor that is a suitable size for your air tools and can deliver the correct CFM may be more cost-effective. This depends significantly on each case, you may have a neighbor who has an air compressor that you can borrow with ease whenever you need the additional CFM, and so, that would be a more cost-effective method.
Duty cycle is another important consideration that you must understand so that if you’re obtaining a second compressor, it has the same duty cycle like the current one, ensuring neither exceeds its rating and overheats, causing damage and premature wear of components.
After obtaining a second air compressor, and you’ve connected it using the method described in this article, you will need to adjust the pressure switches to ensure that the gap between them is not too big. If that is the case, one of your air compressors will be doing the majority of the work, starting and stopping far more frequently.
This will lead to premature wear on the compressor working extra, meaning you will need to conduct additional maintenance, and undoubtedly this will have a shorter life span. In an ideal situation, to achieve the full potential CFM of the combined air compressors, both cut-in and cut-out pressures should be the same.
But, it’s likely that you won’t always need the full potential of the system so it can instead be recommended that you have one of the compressors cutting in and cutting out at pressures 5 PSI lower than the other.
This results in you having primary and secondary air compressors. And, an important consideration here, is that some air tools may only draw air from one compressor (the primary), and so, it is recommended to periodically adjust the pressure switches of the compressors so that one is not always doing ALL the work!
If you have air compressors that are the same make, model, and size, then it’s almost guaranteed that the two compressors will have the same cut-in and cut-out pressures already, so you have no synchronizing issues to deal with! In theory, both air compressors should work approximately the same amount, depending on the tool requirements.
FAQs (Frequently Asked Questions)
The best way to connect air compressors together is by connecting each compressor output to a manifold (typically a tee). It’s crucial that check valves are installed between the outputs and the tee to ensure that air does not flow back into either compressor from the other.
Yes, piggybacking two air compressors together by connecting them to the same line via a tee, will allow you to provide greater amounts of airflow to meet higher demands.
It’s not recommended to try daisy chain air compressors as this involves taking the output of a compressor and running it into the input of another air compressor. It’s better to connect both air compressor’s outputs to a comment tee and then have a hose connected to the output of the tee.
In general terms, the easiest way to manage multiple compressors is to manually set the cut-in and cut-out pressures in a cascade arrangement. All the pressure bands should be the same but they may be offset slightly.
Yes, by adding a second air compressor you now have the addition of two air compressors CFM ratings. If the compressors were the same rating, you would have double the CFM. It may be that you have an 8 CFM air compressor and you add a 5 CFM air compressor, so you’re resulting combined CFM will equal 13 CFM (8 + 5).
If you have any questions about connecting 2 compressors together, please leave a comment below, so that someone can help you!
How would I go about connecting a third compressor? would it be enough to add a second tee to connect a line + check valve from the third compressor?
I’ve also seen a 3 way manifold like this:
https://www.amazon.com/dp/B078W2FZNZ/
Ok, first off this is a great website, thank you. A lot of these entries are about 98% similar but no two are exactly the same. It would be awesome if any one could describe, diagram or link a description for running two dissimilar compressors to an auxiliary tank. The aux tank would be the ultimate source of air for operations.
My exact situation is a primary 15.7 @ 90 PSI, 60 gallon, 2 stage (Quincy 230 volt/30 amp) and a secondary 5.1 @ 90, 27 gallon (Husky 15 amp). I’d be routing them to a reconditioned 40 gallon auxiliary tank. My goal is to be at or above 18 CFM consistently. Secondary to that I’d like to minimize the run time of the units.
Any description to optimize that scenario is appreciated.
I realize this is an old post, however, I am having some trouble understanding the combined volume. I am looking to achieve 12 cfm @ 40 psi for painting. I learned last year how important a check valve is when connecting two dissimilar compressors. Now I am having trouble grasping the concept of adding the cfm to achieve the desired output volume unless BOTH compressors are constantly running the same pressure at the same time?
For example: Primary is 6.3 cfm @ 40 psi w/ 150 psi max & Secondary 7.1 cfm @ 40 psi w/ 125 psi. Both now have a check valve prior to the “T” and with regulator settings a side, how can the output volume be added together unless BOTH compressors are constantly supplying equal amounts of air to the tool?
I don’t see how this can be achieved when nothing else about the compressors is equal? I learned that w/o a check valve while using a regulator to match the secondary compressor, it was still nearly impossible to equalize the air pressure resulting in of the two constantly purging air unless a tool was constantly in use. Even then, how can I be sure each compressor is indeed suppling 100% of it’s cfm unless their pressure is EXACTLY equal? How can the pressure equalize between the two with a check valve restricting air back into the other tank? And even if it could, like you said, the air need to be supplying the tool NOT the other tank.
I hope I am just over thinking this? I’m sure as the variables increase so does the mathematics but my main concern is how even the smallest drop in cfm will effect the flow of paint at the tip?
I am hoping you can help me understand this because I am cursed with the need to know why, not just HOW something works. However, I find any unforeseen problems in the future are much easier to solve this way. Thanks in advance and any help would be appreciated. Paul
Paul, did you ever get an answer? This is the exact situation I’m searching to resolve. I’ve got a primary 15.7 @ 90PSI, 60 gallon, 2 stage and a secondary 5.1 @ 90, 27 gallon. I’m running them through a 40 gallon auxiliary. My goal is to be at or above 18 CFM consistently.
Would it be a good idea to disable the pressure cut-in/out switch from compressor ‘B’, then run a jumper from the pressure switch on compressor ‘A’ over to the motor leads on compressor ‘B’? That way, when the overall pressure in the system drops below the low threshold, then both motors run at the same time. Assuming the single switch has the amperage rating, or you use a relay. Or is this not a good idea?
Possible if enough amps and current in the power supply. Often folks let one compressor take the work of starting and supplying air and only have the second come on if more air is necessary to keep up. The trade off is maintenance, cost of power etc. The bottom line is that the page offers one set of process to get more air, but each owner can certainly modify the idea to suit their need. Just keep it safe! Good luck.
Hi, I have two 6 gallon Porter Cable pancake compressors. To spray wall texture, it uses a lot of air. If I were to hook up a hose between the two, easiest with a male to male hose, and hooked up a hose to one to run to my texture hopper, would this work? I believe in theory that they may both turn on at some point, but the air in both tanks should remain the same. Does this sound feasible? Thanks, Tim
Well I spent an hour reading about 40 or 50 of these and never ran across my question. All of them talked about putting an inline check valve and coming into a t. None of them talk about connecting the two compressors and having the air come out of just one of the compressors. If it was in there I must have missed it or not gone far enough
If you connect two compressors, and don’t put a check valve in one of the lines, all of the air will flow out of the unloader valve of the compressor that isn’t running. They will not synchronize, they will run at different times, and then, the one that’s running will run and run and eventually overheat and / or burn out.
The supply line to the spray texture gun won’t change in size, therefore, the same flow will come through the line at the set pressure and will not increase to improve the spraying of the stucco.
What is the recommended supply flow and pressure to operate the spray gun?
Well there is not a set pressure. It depends on the thickness of the spray texture and what size tip you are spraying with. These smaller compressors charge to about 135 PSI and then I have an air valve at the gun and I just open it up until it’s sprays the correct pattern that I want.
What would happen if I were to leave one of the compressors turned off and only ran one to keep the pressure in both tanks up? When I’m running it and spraying the texture it might only be 5 or 10 minutes so it’s not like it runs all day this way. I also don’t do this on a daily basis but maybe once a month.
The pressure is one thing. The other is the flow at that pressure.
Two tanks means that it will take longer for the compressor to come back from air use.
And, as I said “If you connect two compressors, and don’t put a check valve in one of the lines, all of the air will flow out of the unloader valve of the compressor that isn’t running”.
Tim, I’m a bit puzzled by your question given that the details on this page talk about exactly what you are trying to do. Please re-read the page, and if you still have a question, please do add a comment.
I have a 5 hp screw compressor with a 60 gallon tank. It is set at 175 psi. I have a second compressor that is a 3 hp with 60 gallon tank set at 135 psi. I want to hard line both of them to a 120 gallon tank (it is rated for 200 psi and won’t be going that high any way) and run my tools off this tank. Do I need any check valves for the tank that has the lower psi setting ?
Hi Jason. So are we to understand that you are linking the two compressor tanks to the one larger 120 gallon tank?
Issues you’ll want to consider are run times of the compressors to be sure that they don’t exceed their duty cycle as you are filling a much larger tank, and also whether or not one compressor will run all the time but the other doesn’t run as often.
In terms of plumbing, anytime a compressor is off – as in it’s stopped on high pressure cut out – the line to the tank is typically open to atmosphere. That means that if one compressor is running, and the air from that can flow to the off compressor, air will exit the unloader valve there, rather than going into the tank. That’s why a check valve is required in the line from the compressor and before the tee to the other compressor and new tank.
Hope this helps.
i have a compressor “A” running at 14.5 bar outlet 14000 cfm. supplying to line A
another compressor ” B” with 10.5 bar outlet supplying to line B.
Iine A compressore is on load for only 30% of the time.
Line B compressor is on load for almost 60% of the time.
Can i interconnect both with a control valve to utilise the air form compressor A for Line B so that the load on the compressor B comes down?
Yes. Some logic and hardware will need to be involved to achieve the goal, but sure, it’s possible. You’ll also have to reduce the pressure from A before it enters the line for B, of course. If you are seeking explicit instructions, you’ll need to hire a local expert to provide that for you where you are.
Dear sir
Thanks for taking time to respond.
We have consulted a vendor who adviced us to go for a simple control valve with suitable “kv” and a pressure control loop at the upstream.i.e at 14 bar line. His philosophy is that if the upstream pressure is more then the valve will be opened and source to the lower pressure stream.
but we feel that here the compressors in the lower pressure will be in unload condition for most of the time or there could be hunting.
You are getting into the area of air use engineering here Srinivas and I’m not qualified to aid you in designing your system. Sorry. If your local vendor says their solution will work, and it doesn’t, it would be up to them to fix it, wouldn’t it? I am not going to critique a solution of another person. Good luck.
I want to add a secondary compressor to my sprinkler dry system will i have to add a second regulator?
As long as both air compressors end up being plumbed to the same air line, before the regulator, then no, one regulator will suffice.
I had struggled with the same problem – especially when I decided to connect three compressors together, while putting some check valves and adjusting pressure works ok I used this thing to network all the air compressors: http://compressorcontroller.com
Any possibly way that you could add links for a check valve and a tee and what else could possibly be needed for this process?
Thanks
Why doesn’t anyone from this site answer people’s questions. They are definitely making money from this site with all the ads running on the page! It’s shameful to say the least…
It would appear as though you used your time flaming the site rather than reading the information on the pages on this no-charge-to-you service. Please, if you cannot find the info you wish, ask a question on the appropriate page… but first, read the page to do with your compressor problem that already answer many questions about compressor issues over an over. If the ads on the site, which pay for it providing you information at no charge bother you are a “shame”, make your own site. Cheers.
Difficult to do, Zach, as air lines on different compressor makes and models are different sizes. If you Google compressed air check valve and air line tee, you’ll find lots of sources. You then need to pick the type and size that suits your compressor setup.
Hello, I am running two compressors in tandem and everything works fine except the pressure regulator on one sometimes leaks air and hisses. This only happens when running the compressors together, but is fine when run by itself. Is that one regulator bad or something else???
If the regulator setting is below the air pressure in the line downstream from the regulator, air pressure will bleed from the regulator to allow the downstream air pressure to drop to the regulator setting. The solution is to have a check valve in the line downstream of the regulator so that air pressure in the line downstream that may be higher – when the other compressor regulator setting is higher for example – cannot backflow to be vented.
Hello, I have two compressors I’m hooking together and I have a check valve for the secondary but not for my primary. I am painting a vehicle and need the extra capacity, can I get by without buying a check valve for my primary compressor? The primary holds around 150psi, and my secondary holds about 120psi max, I want to keep my main compressor from running all the time and burning up.
Thanks.
If you have only one check valve, and the secondary compressor comes on but the primary is off, the air from the secondary will leak out of the primary instead of going to the tool.
I’ve tried that process but one of the air compressor did not start automatically in cut-in. Even though they have the same cut in and cut out setting..
Typically folks will have a primary compressor and a back up, to kick in when the flow requirements exceed the CFM capacity of the first compressor. With both pressure switches set at the same level, you would think that both would kick on at the same time. We suspect that the pressure switches have a range of accuracy, and even though both are set – or you think they are set – at the same pressure, clearly one reacts faster to the drop in tank pressure and fires up before the other can. And, of course, air pressure immediately starts to rise, and the second pressure switch never reaches the cut in.
That may not be a bad thing though as it defaults to the typical set up for two compressors. Depending on your air use, the air pressure may drop far enough to have the second compressor kick on, assuming its switch works.
If that comes to pass, and you use the compressor(s) daily, maybe every couple of months change the settings on what is the primary compressor to make it the secondary one, so that you get even wear on both.
what if you haVe one tank and 2/ compressor. model tc.20 how wood you do that????
John, yours is a good question, so we decided to add a page about it: http://fix-my-compressor.com/two-compressors-and-one-compressor-tank/ We hope this helps.